- What is the history of pulleys and what are their innovations?
- What material are the pulleys made of?
- The pulleys look very simple, the modifications are rather cosmetic. Is this really the case?
- What is the reason for the higher price of the pulley?
- Is it possible to negotiate some kind of discount when buying?
1. What is the history of pulleys and what are their innovations?
I decided to develop new types of pulleys because the types used were too amateurish and their performance and safety were at a low level. I have been developing pulleys for about 15 years (see pictures).
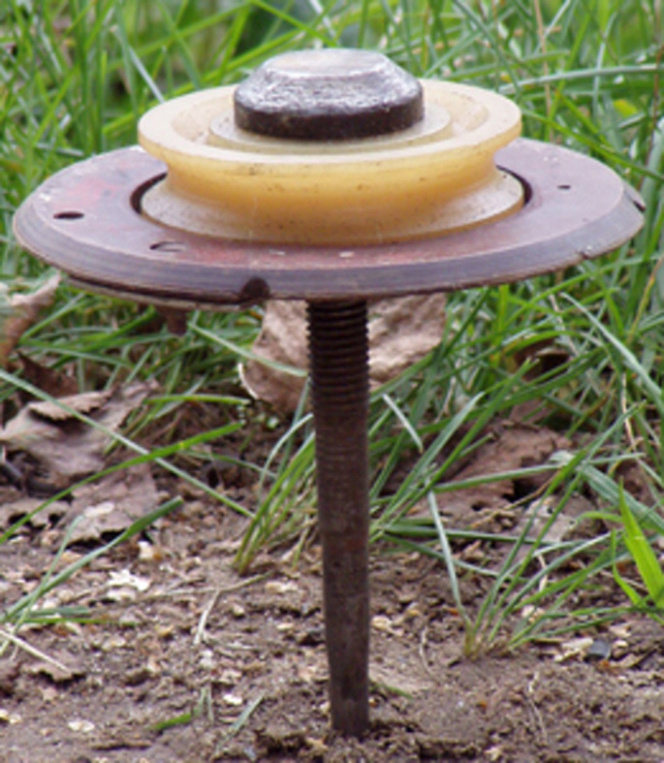
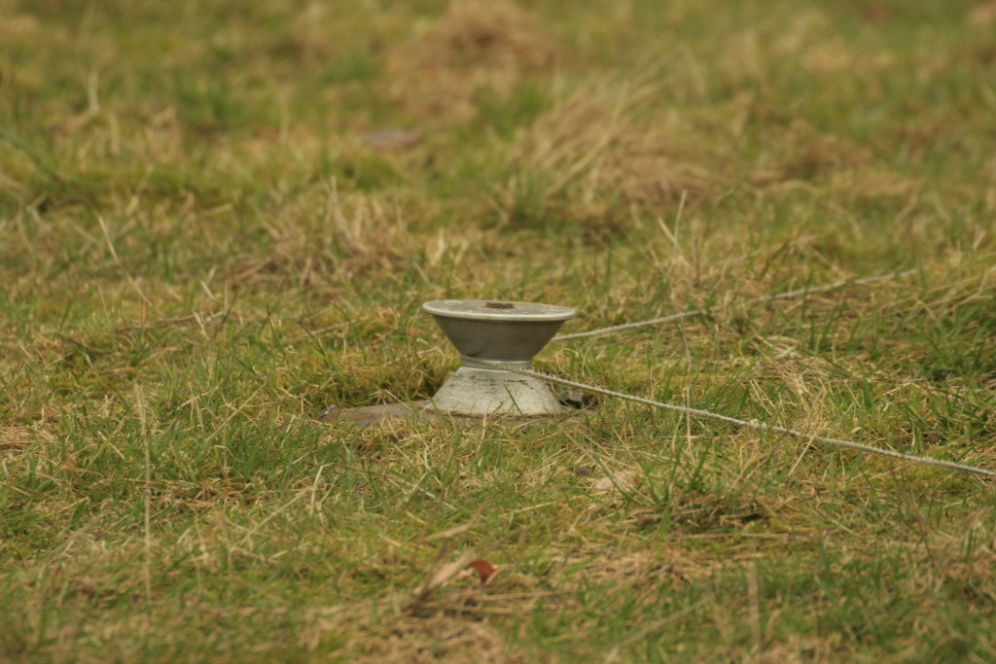
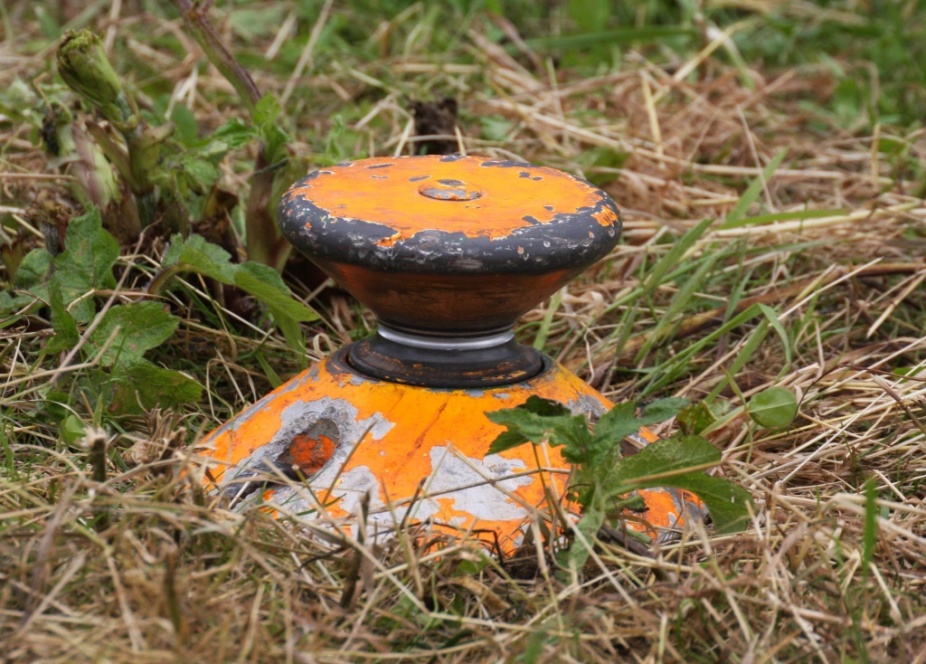
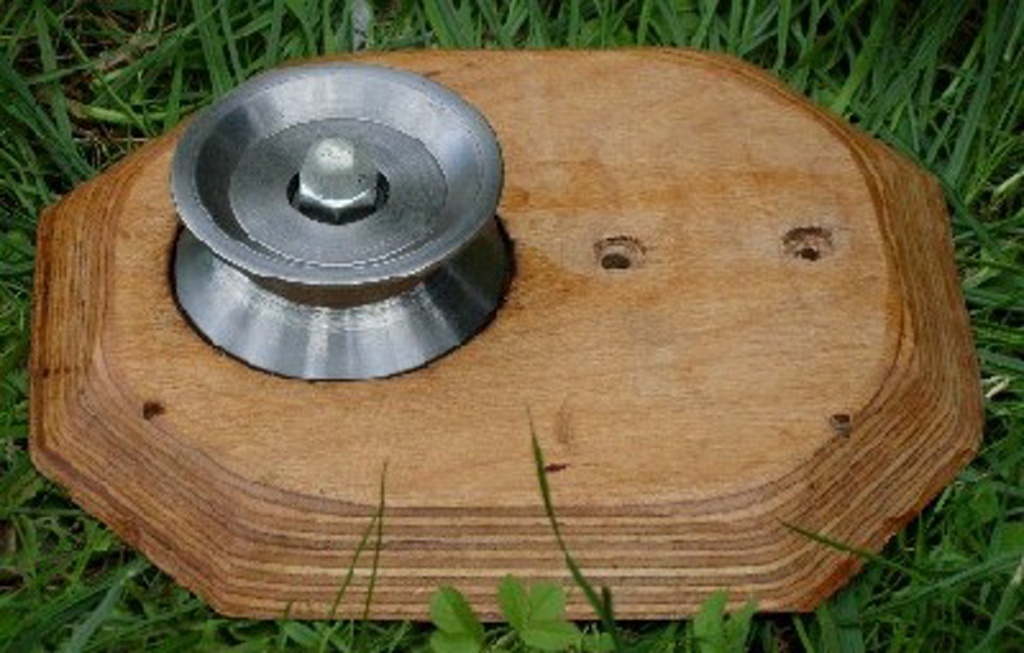
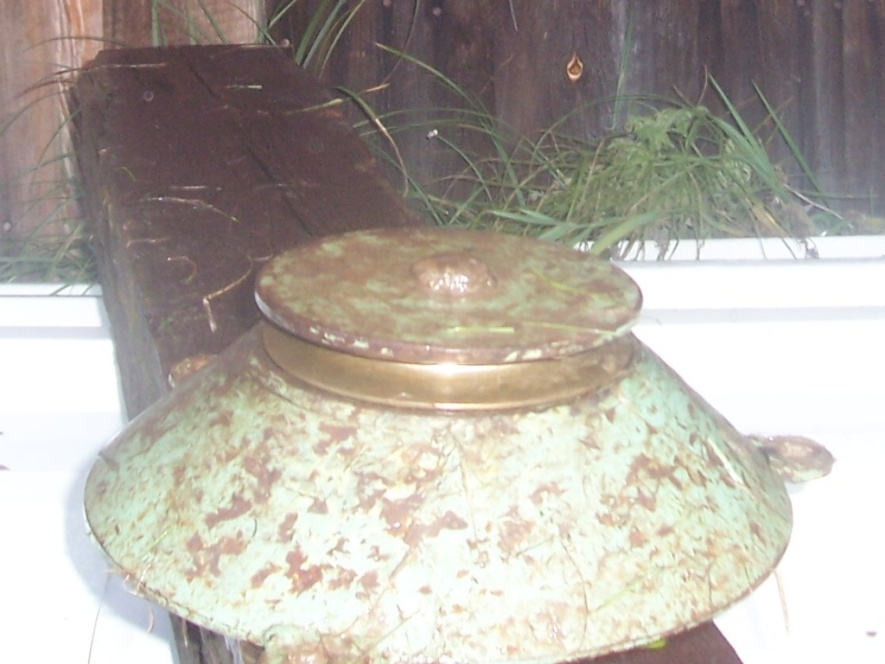
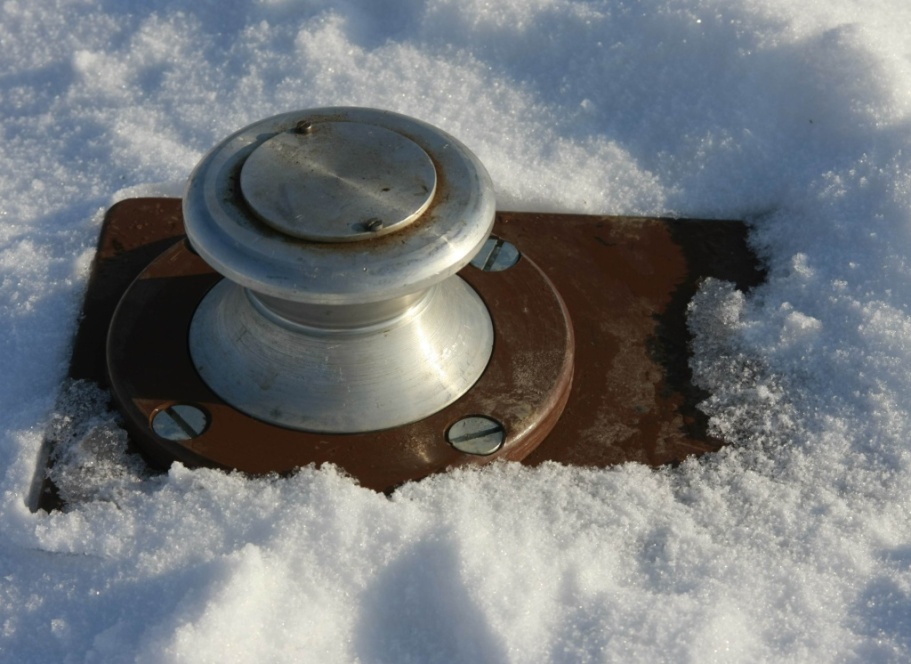
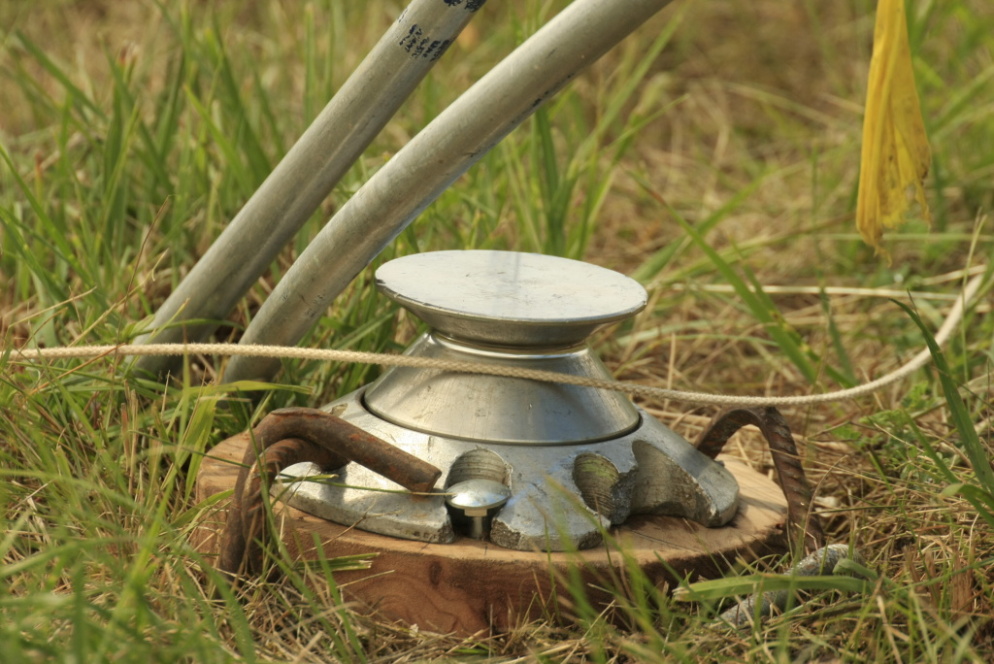
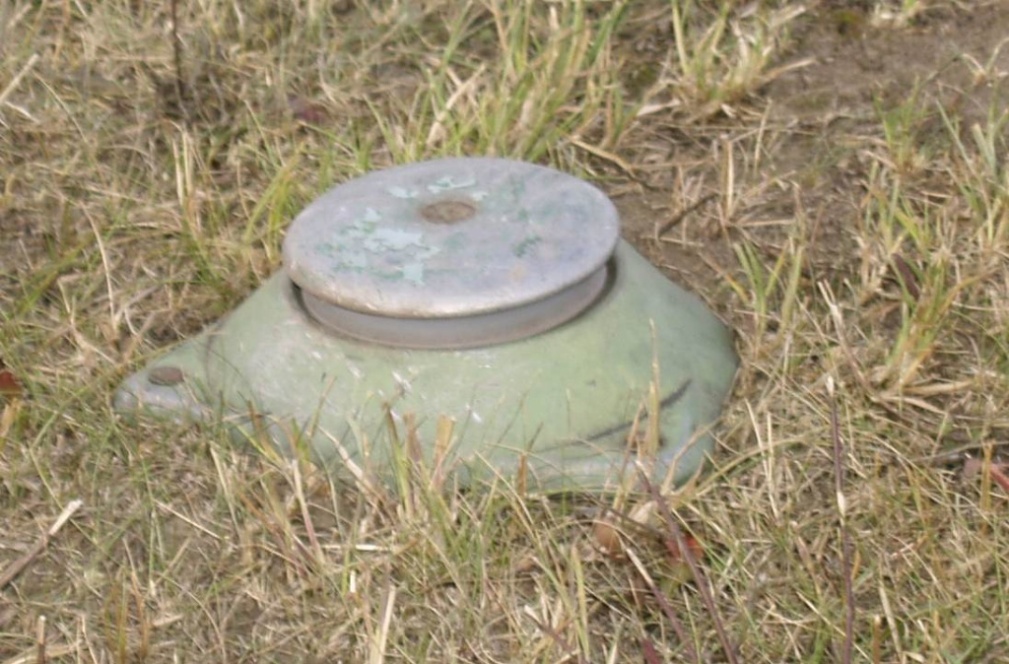
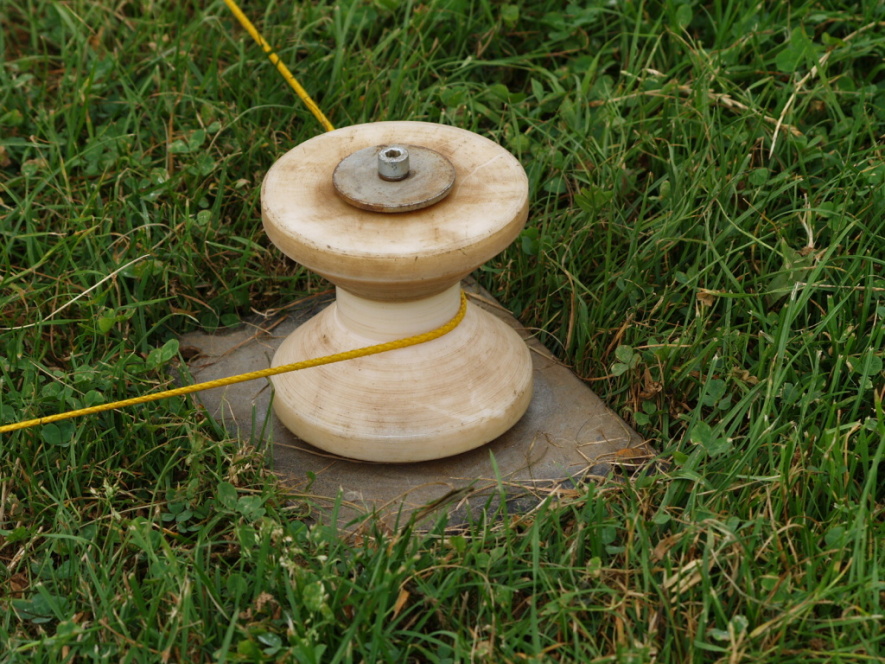
It started first by solving the problem of fixing them to the ground with a single spike. The tops of the first pulleys were not at all like those of today. I solved the bottom part from masonry ladles that were modified by the lathe and welding reinforcement for attachment. The top was made with minibike discs. Anyway, everything was already hot-dip galvanized at that time (see pictures).
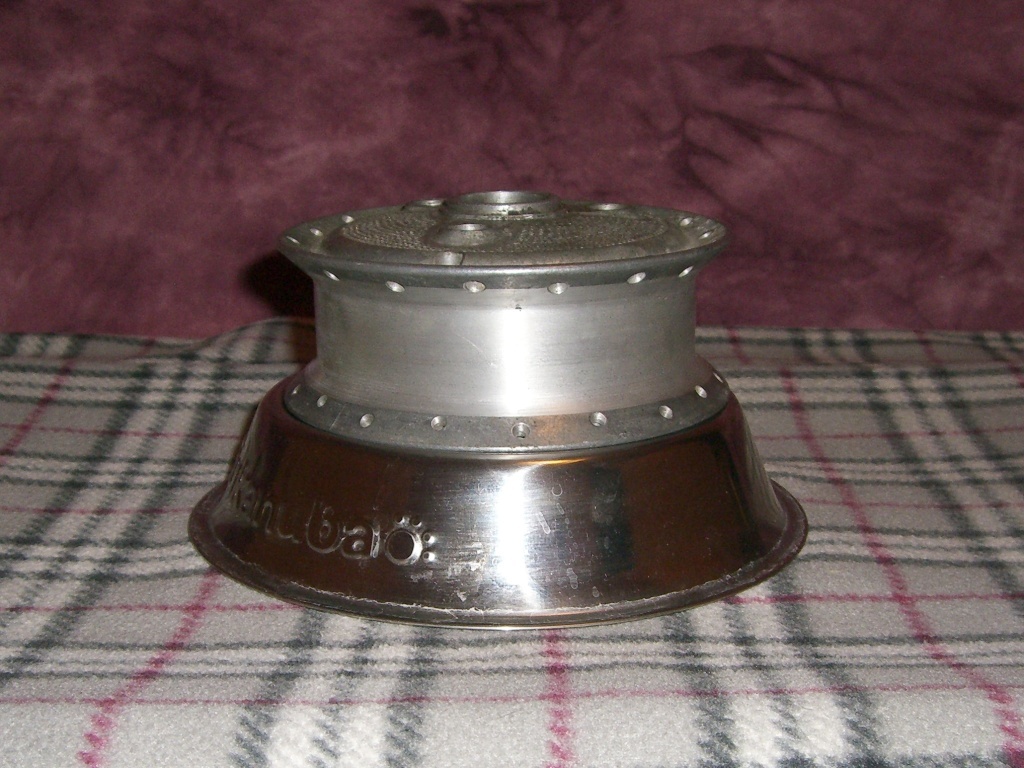
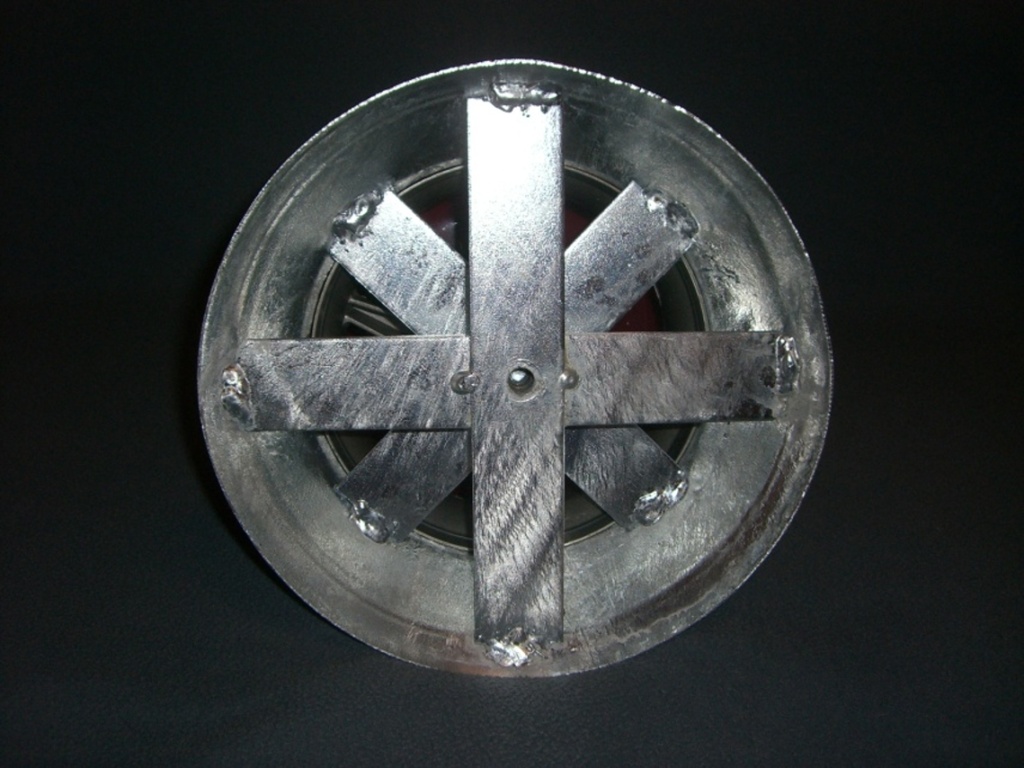
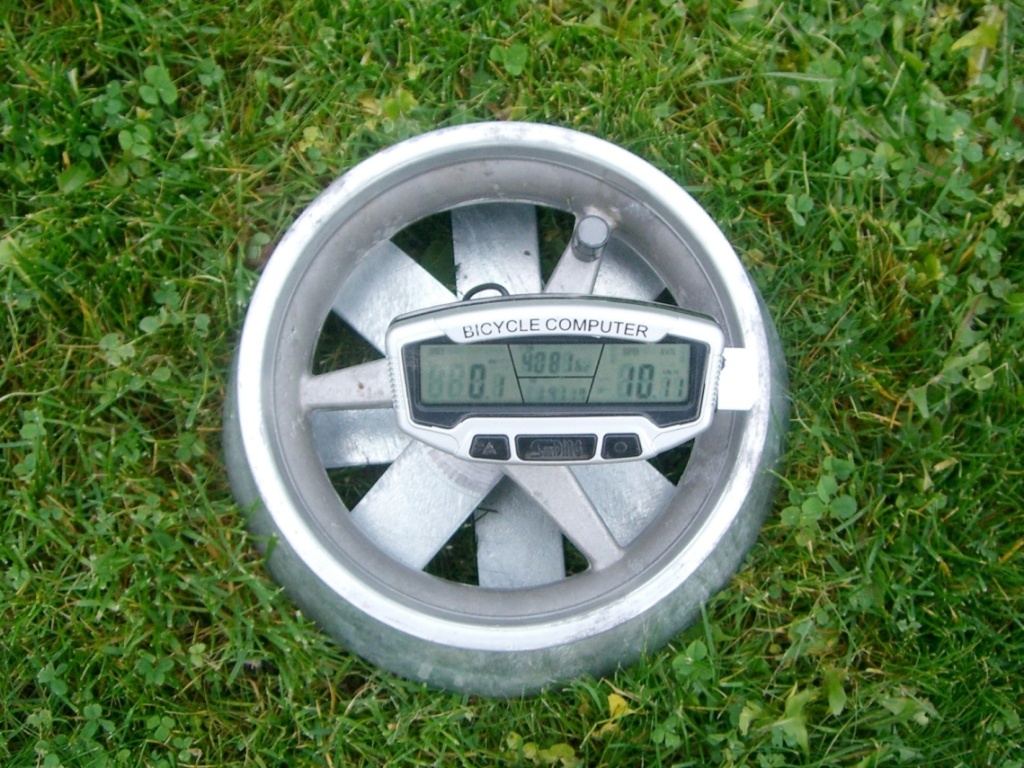
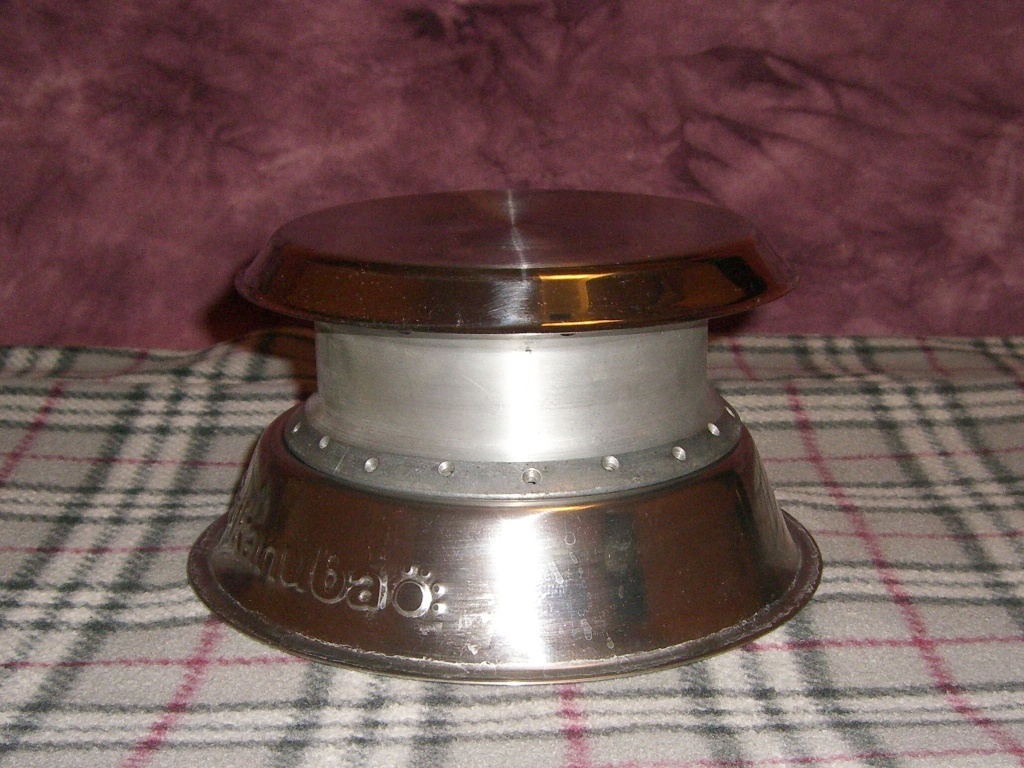
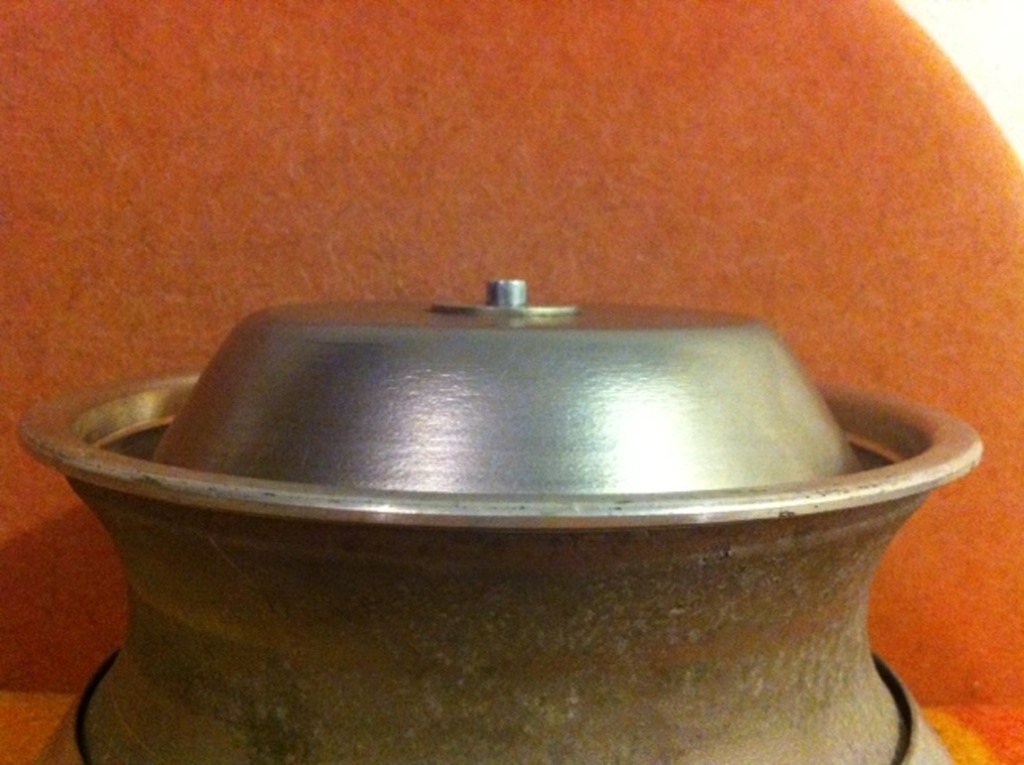
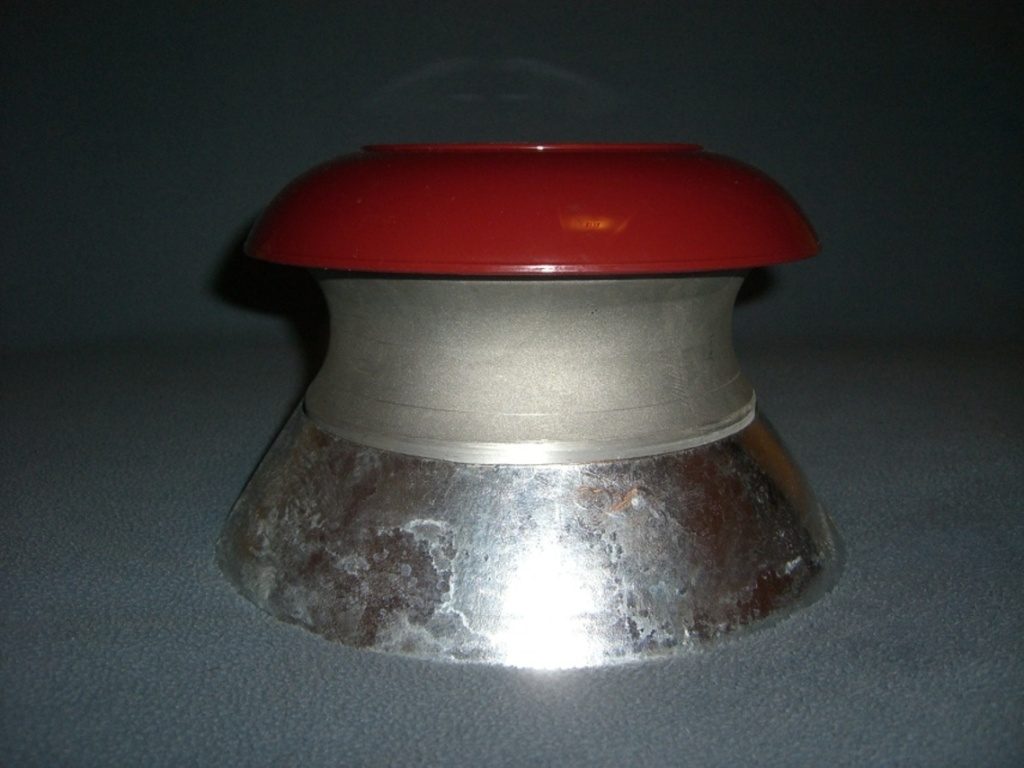
Later on I made a smaller version using discs from minibikes. Incidentally, these pulleys, in several copies, are still actively working today. (see pictures)
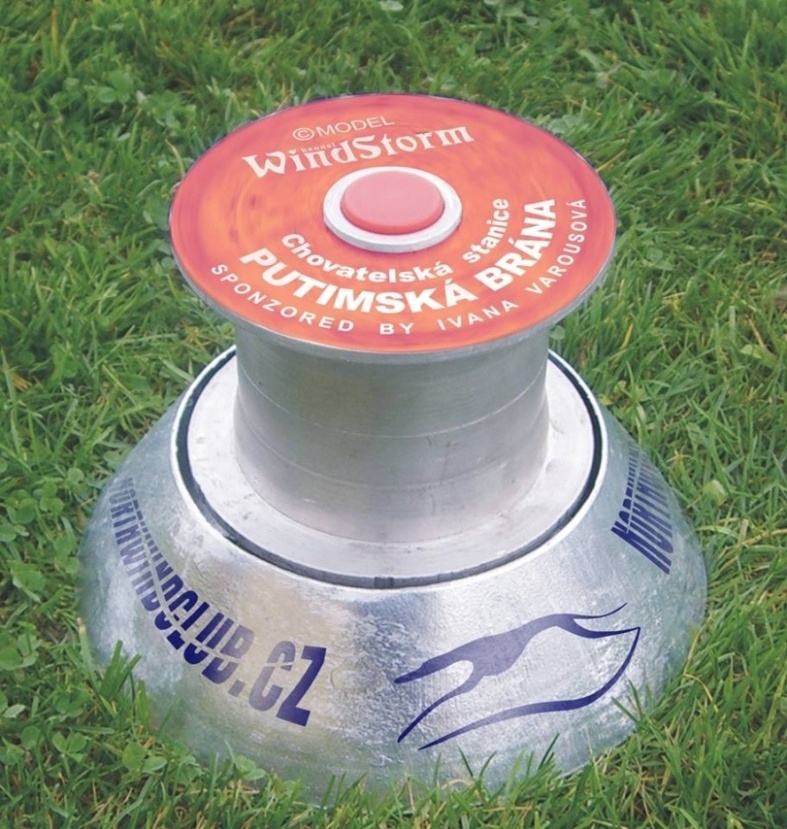
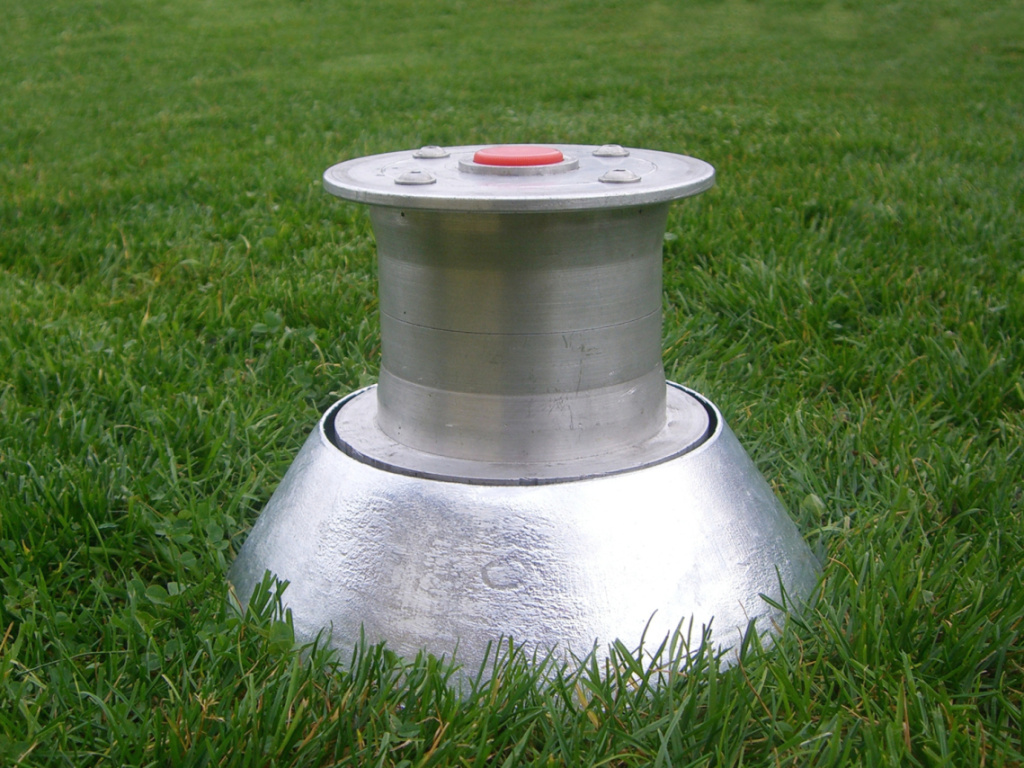
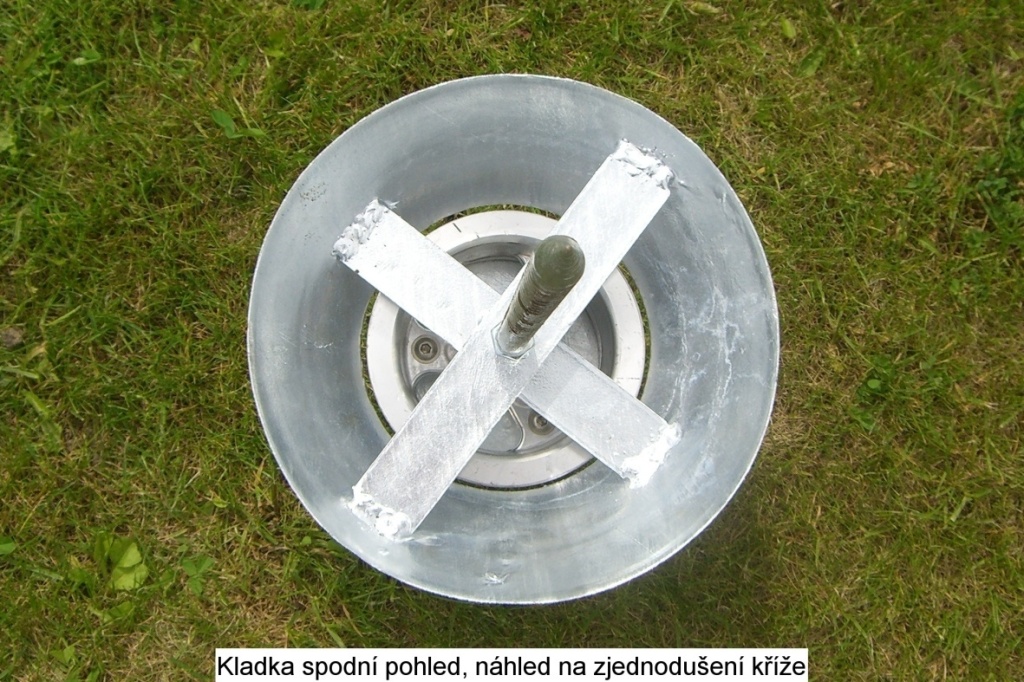
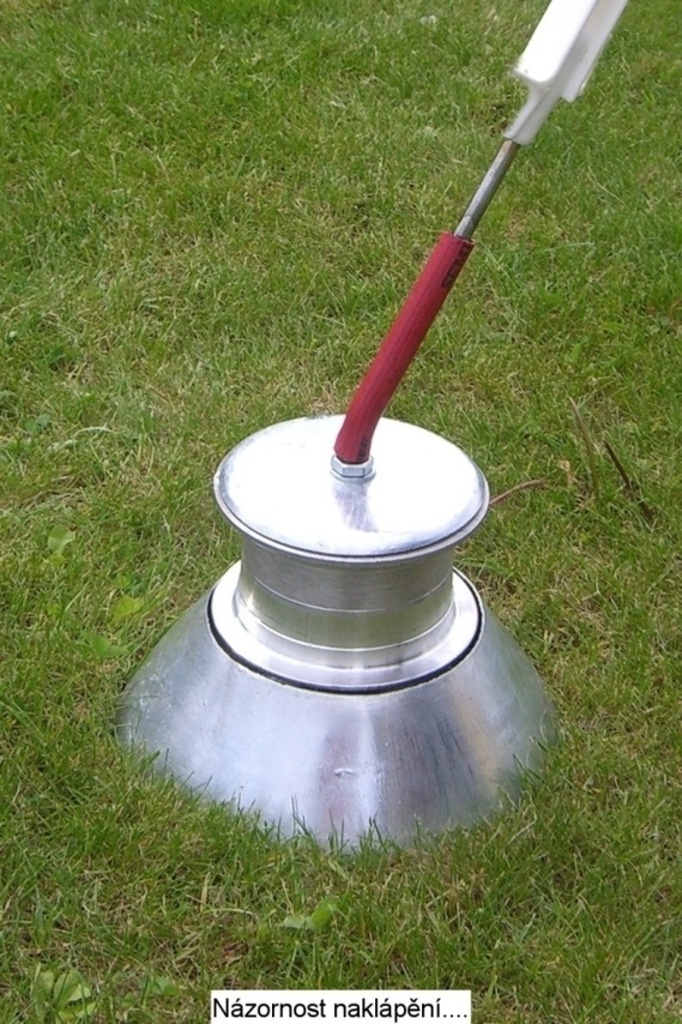
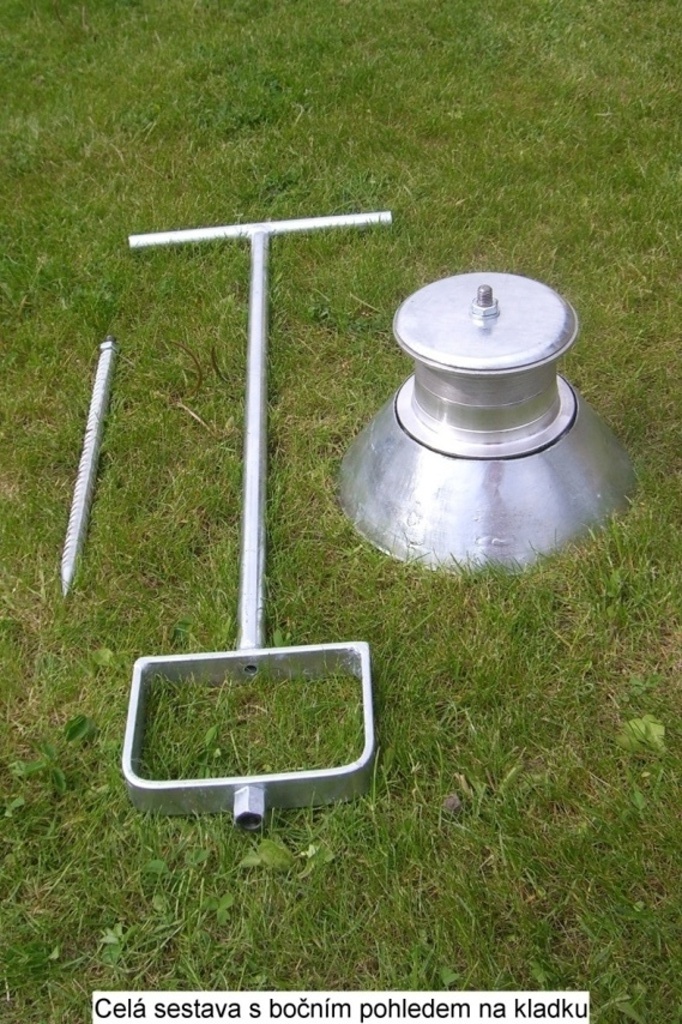
About 10 years ago I made the first pulley with only a rotating center and a top standing part with a protective rubber ring. The bottom of the pulley was made of a steel dog dish. (see pictures)
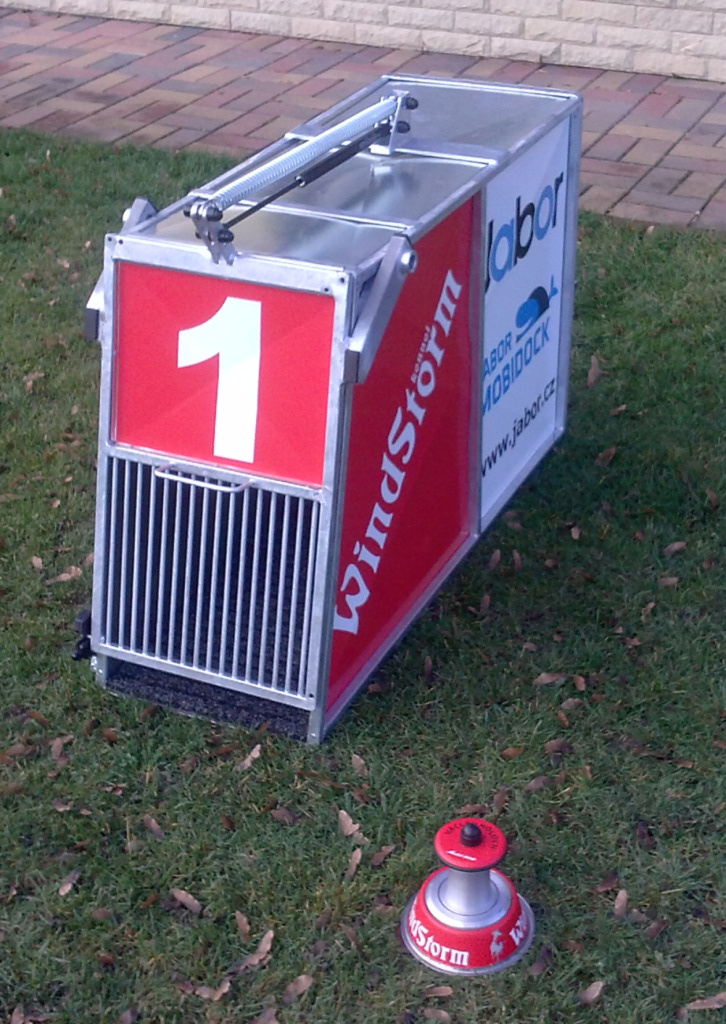
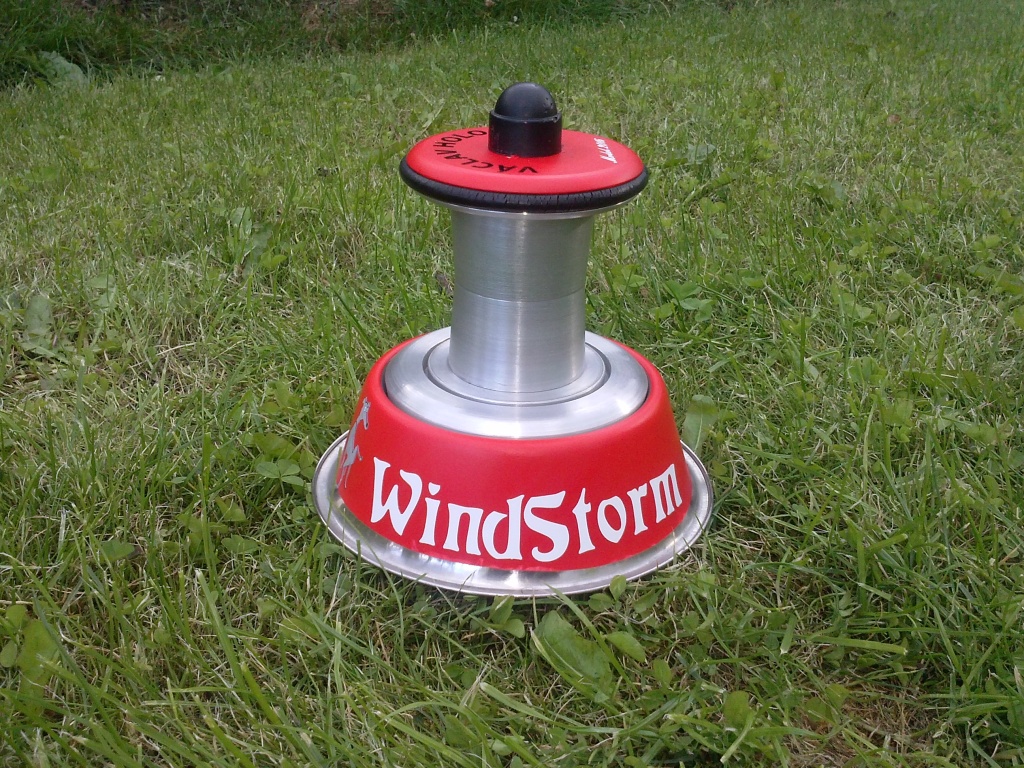
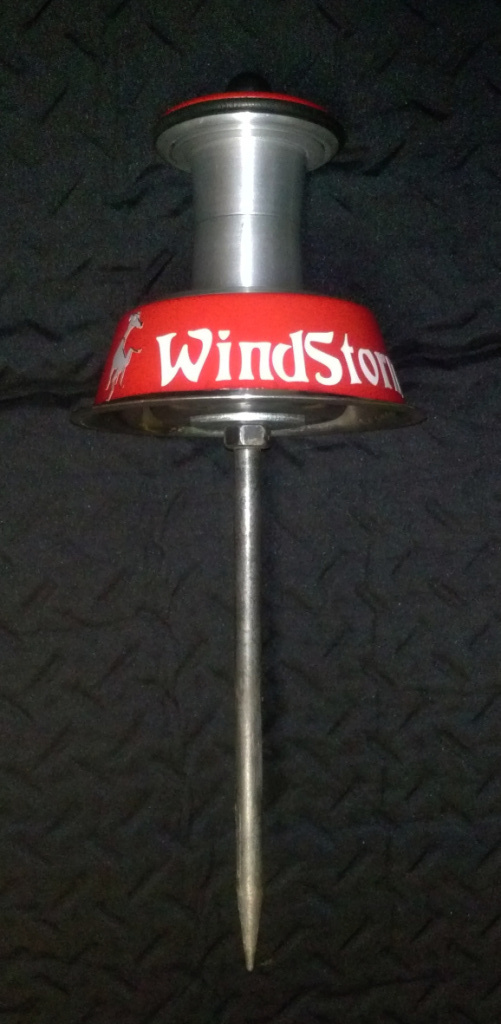
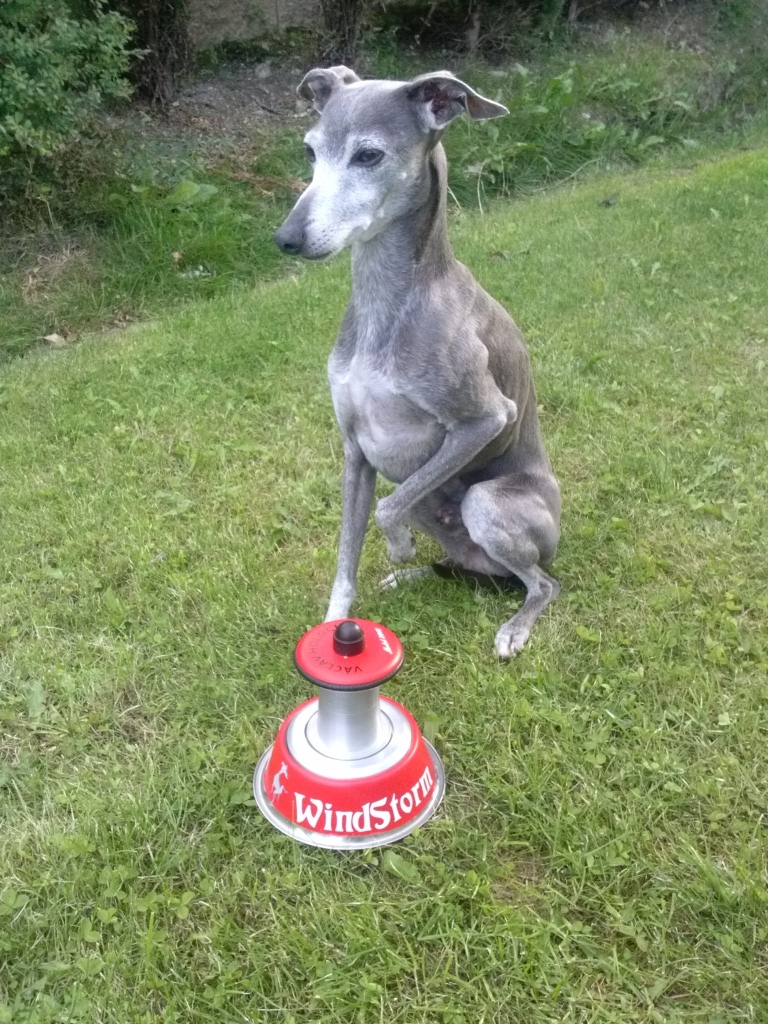
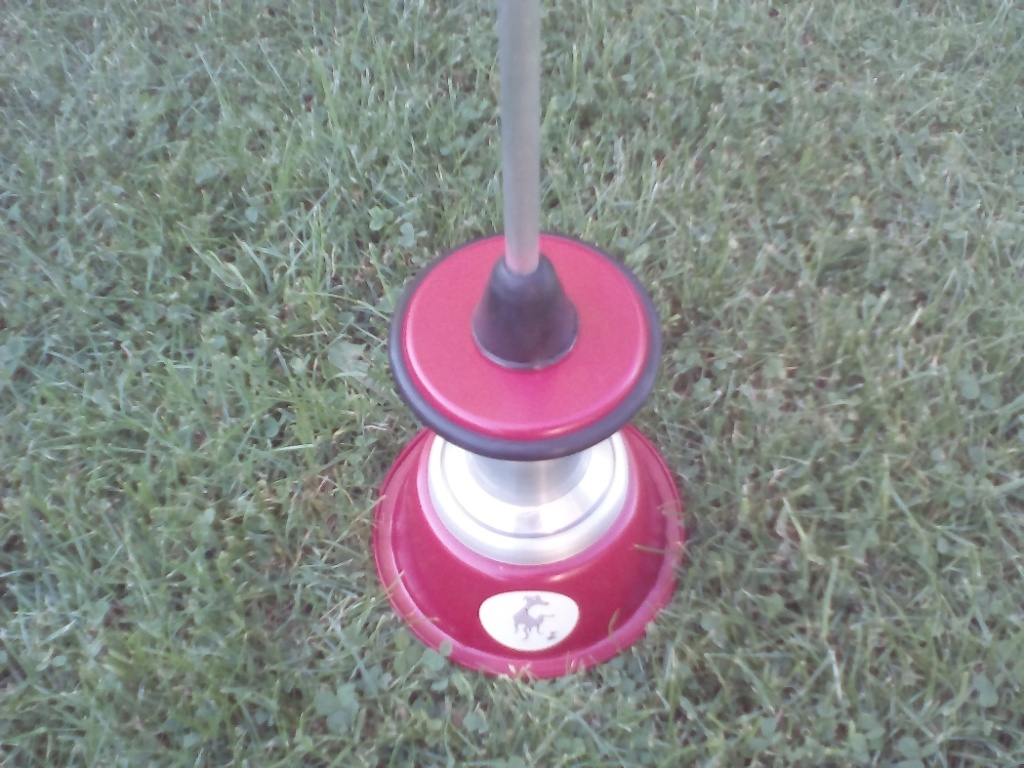
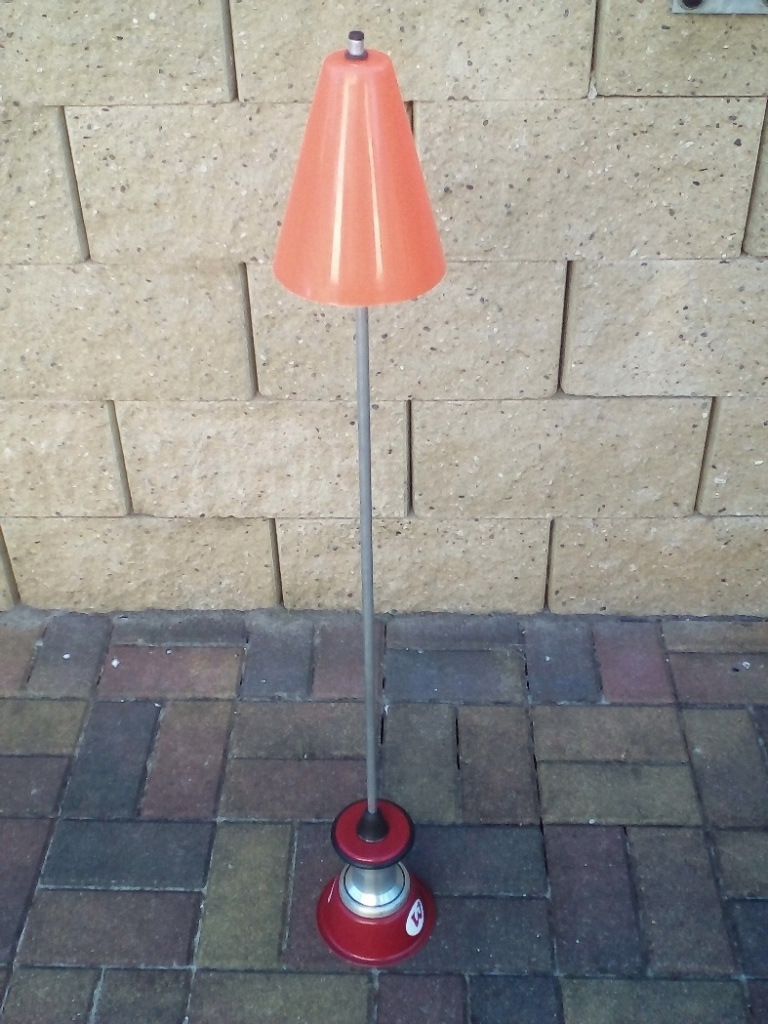
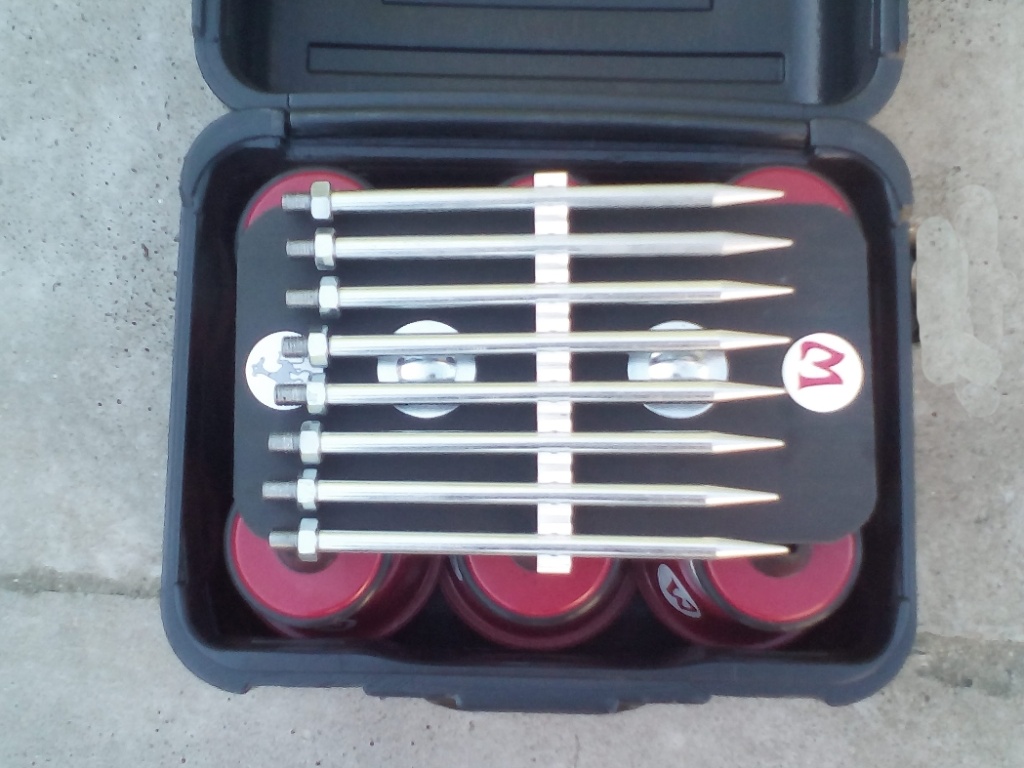
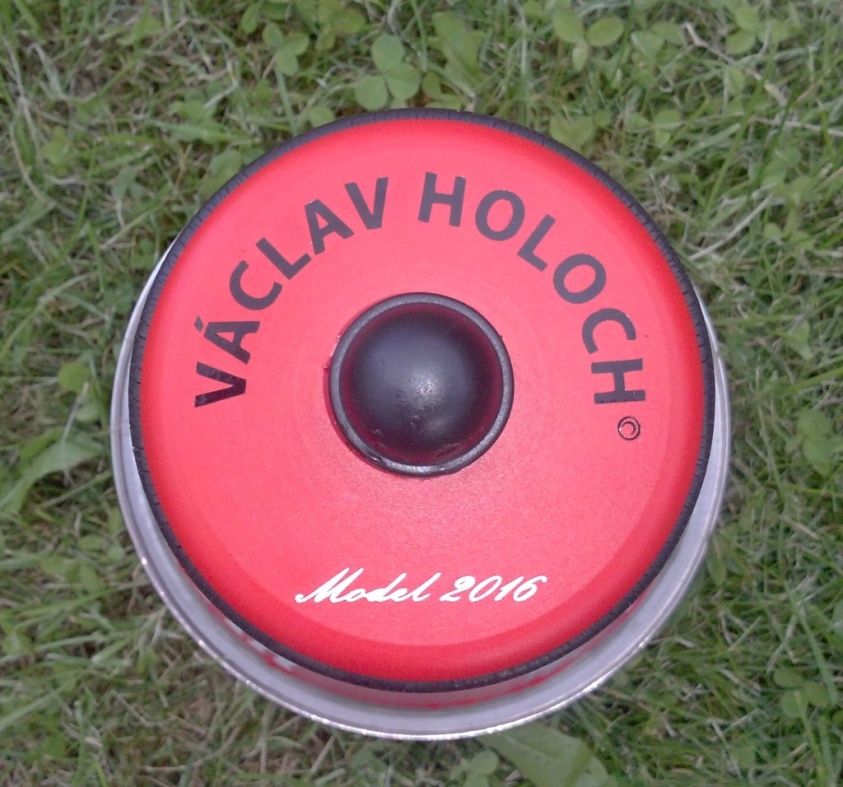
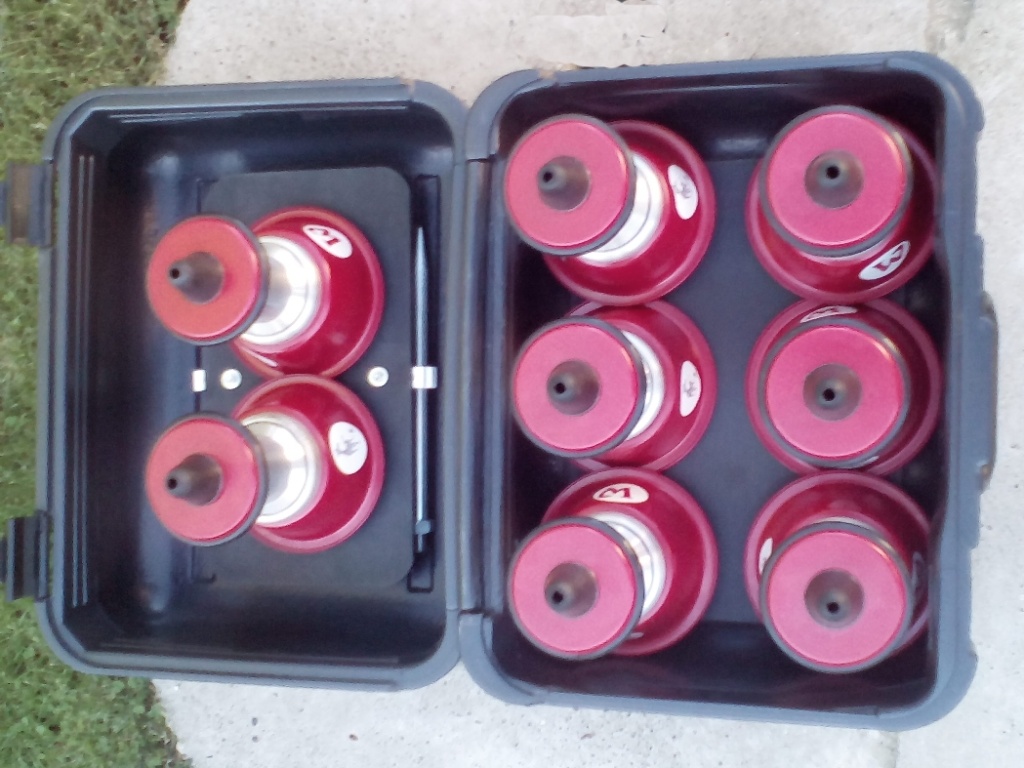
In later years, I found that it was best to make everything even at a higher price, as it would optimize the utility as much as possible. In this way several models were made which I was always convinced could not be made better. Today I know that this is not true (see pictures).
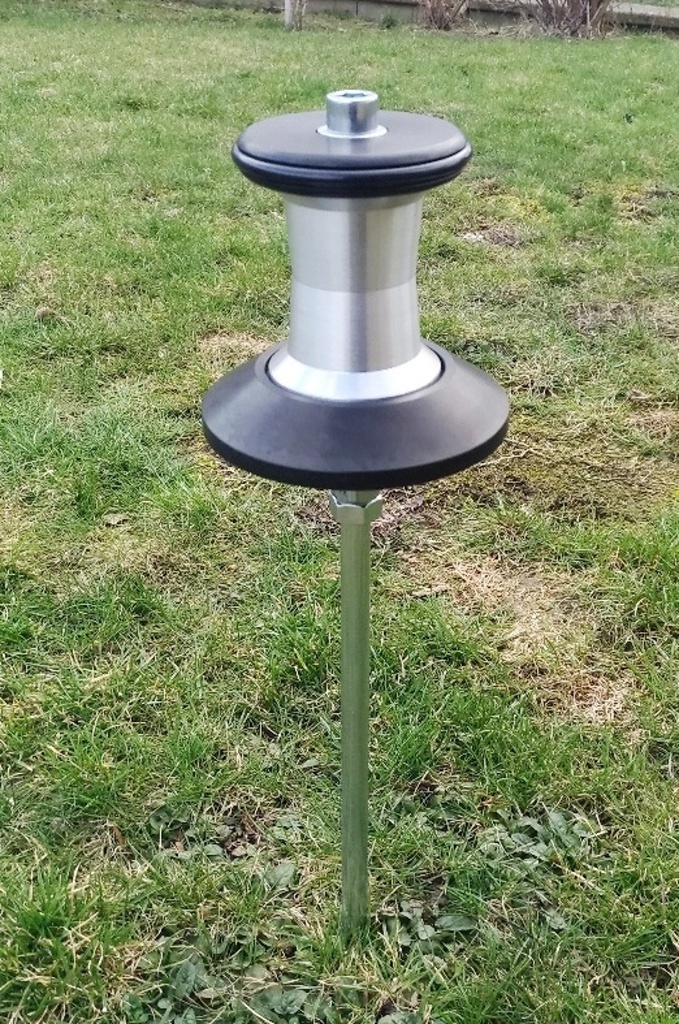

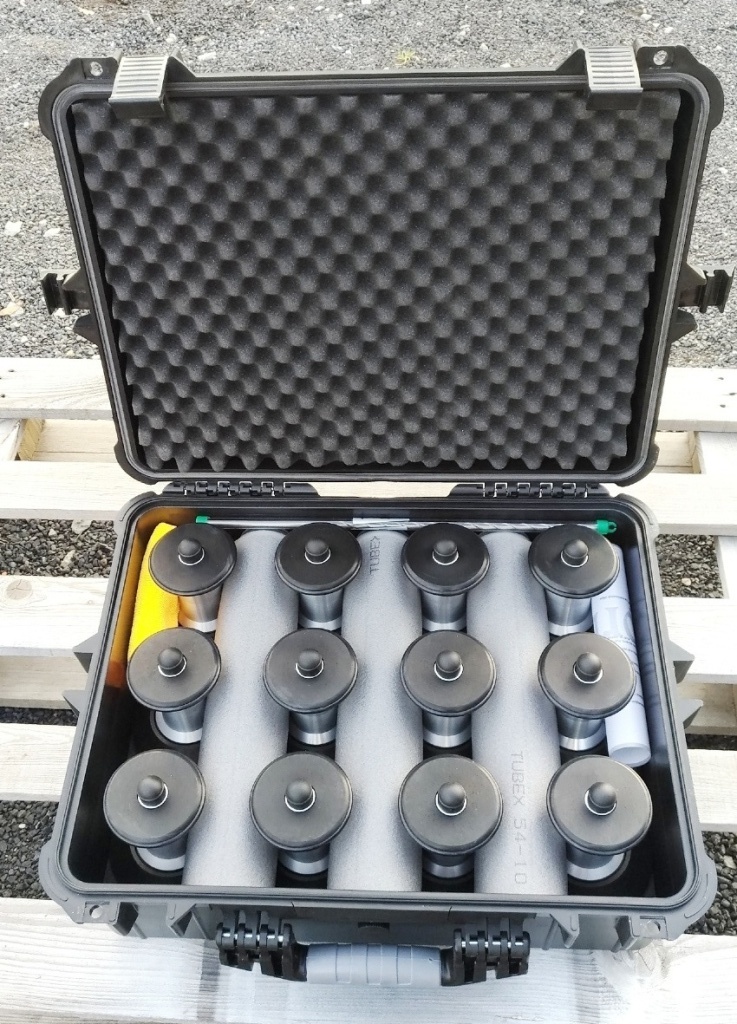
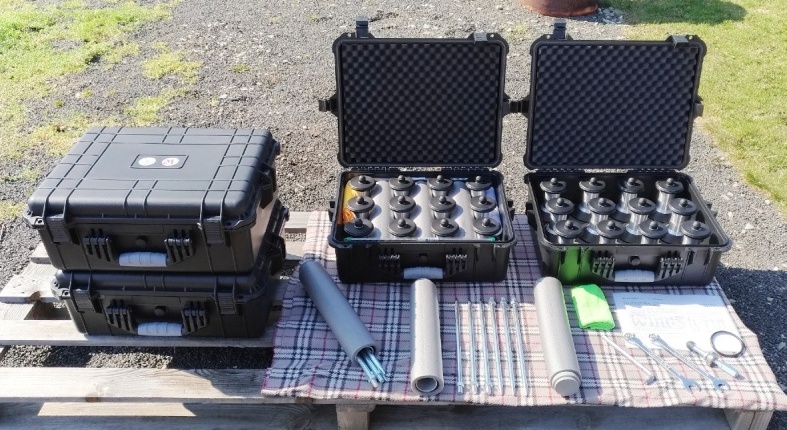
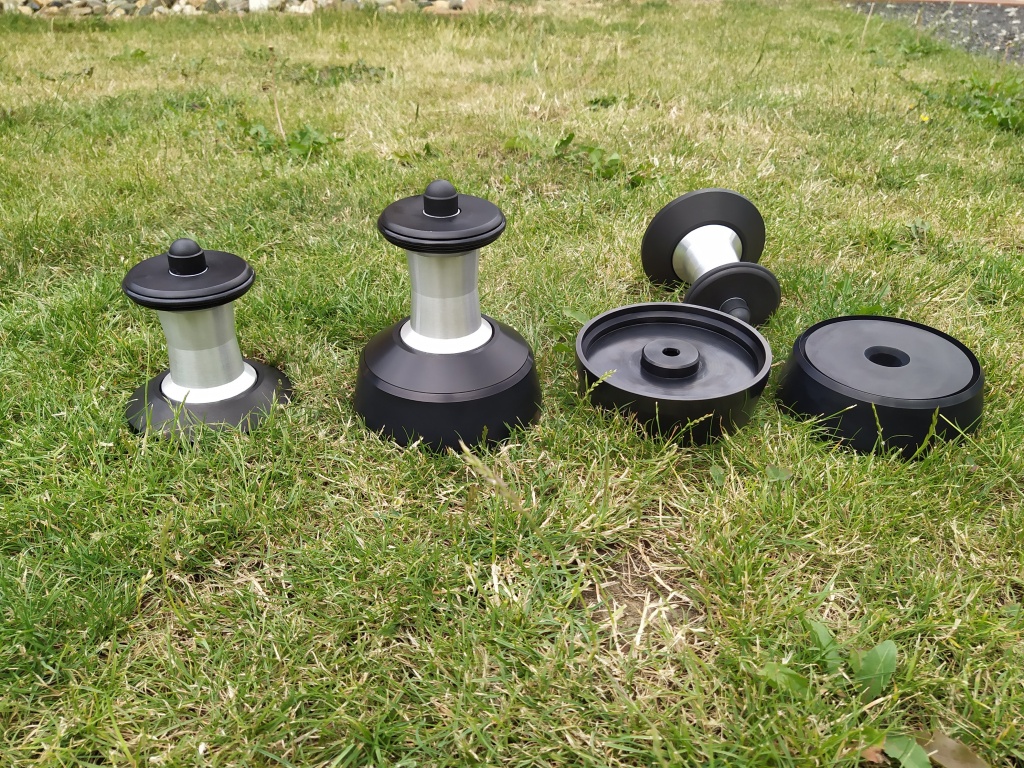
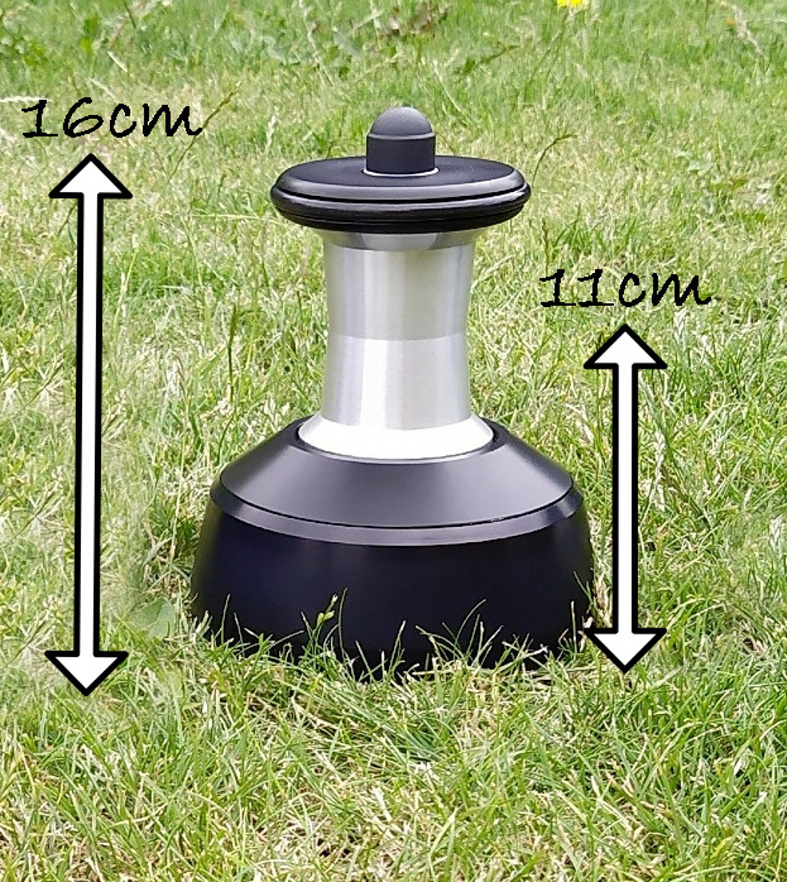
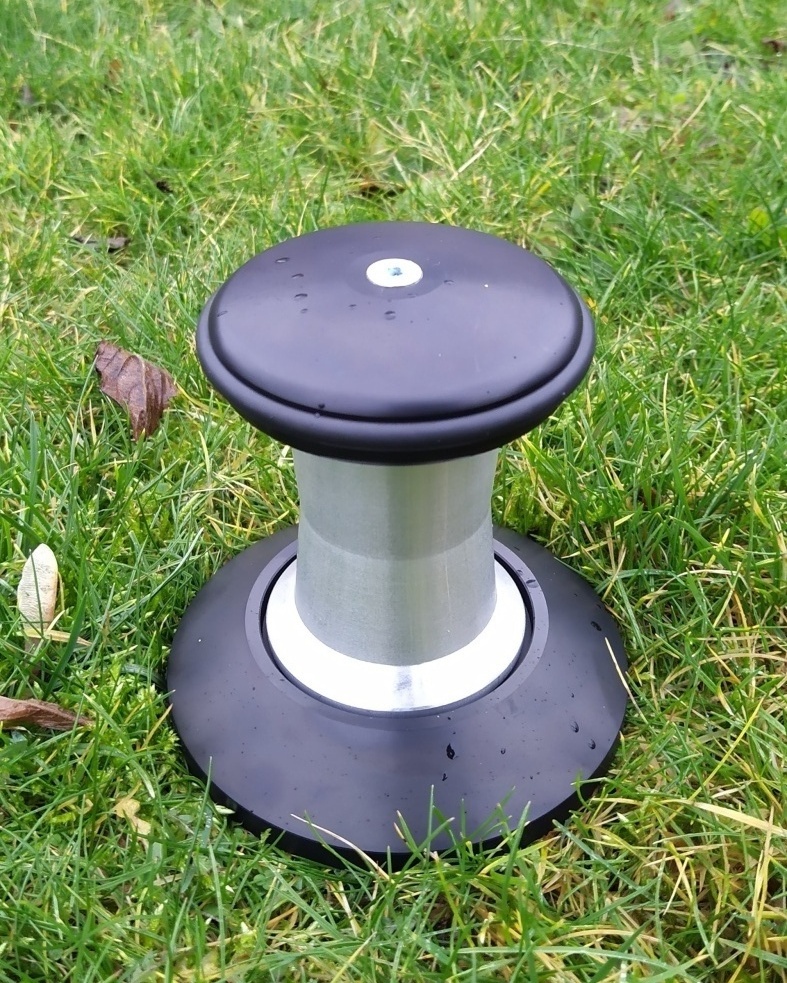
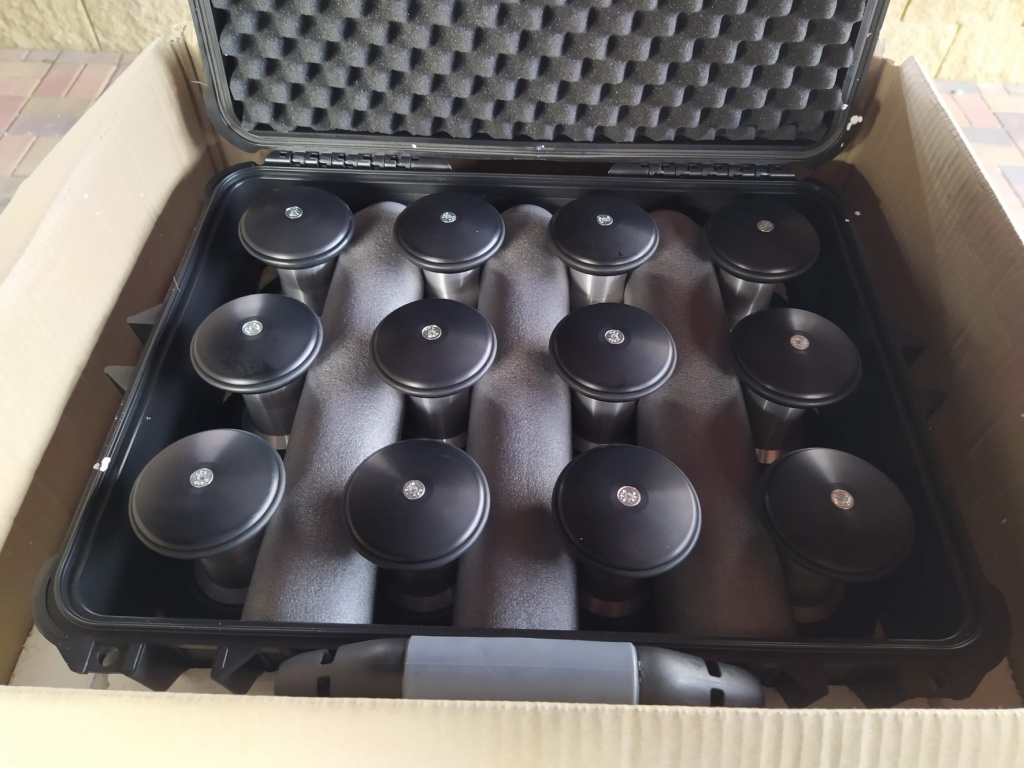
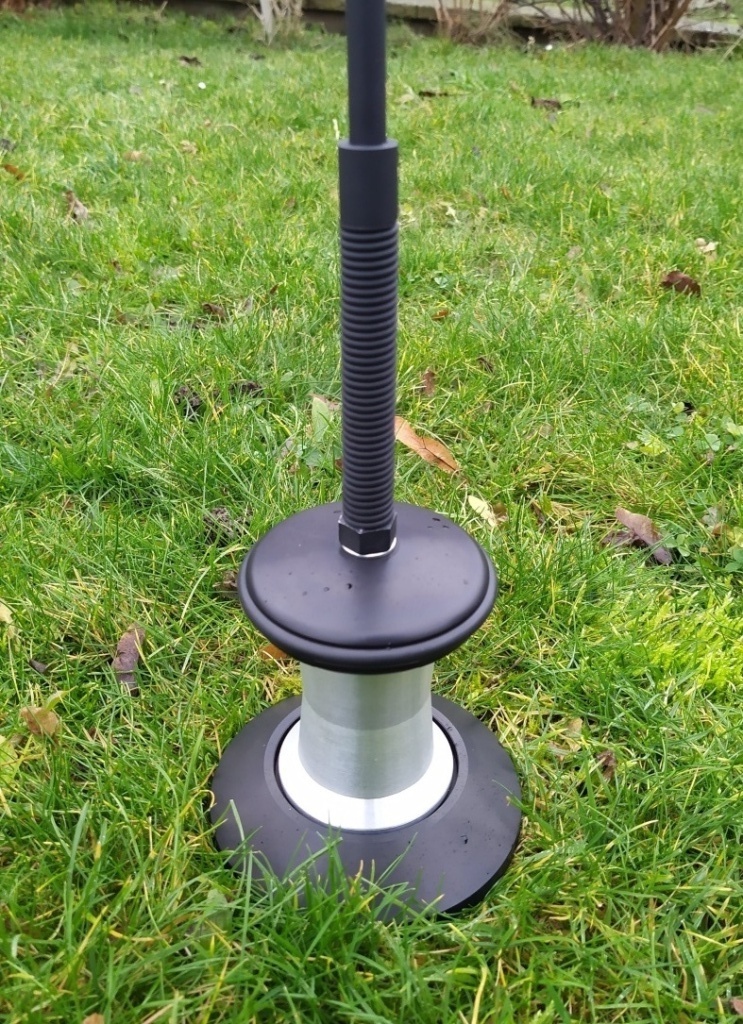
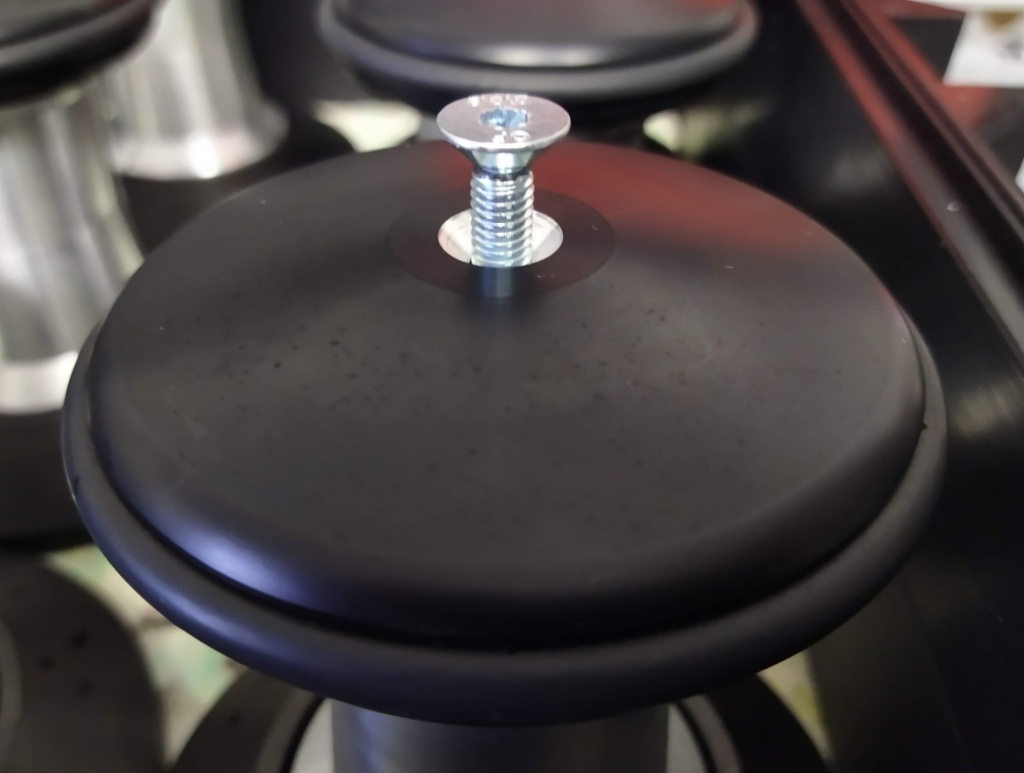
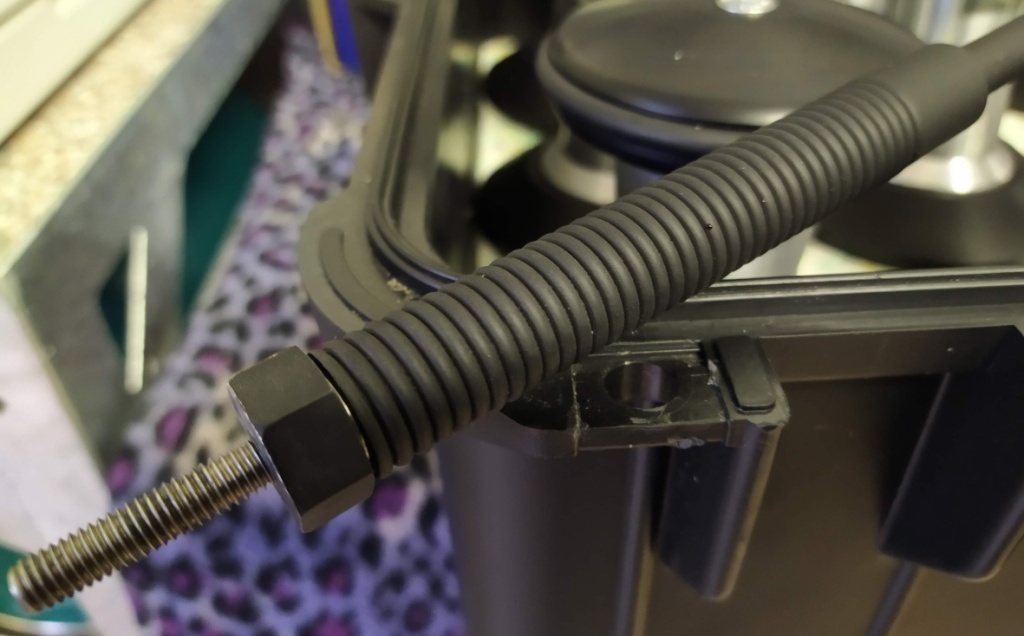
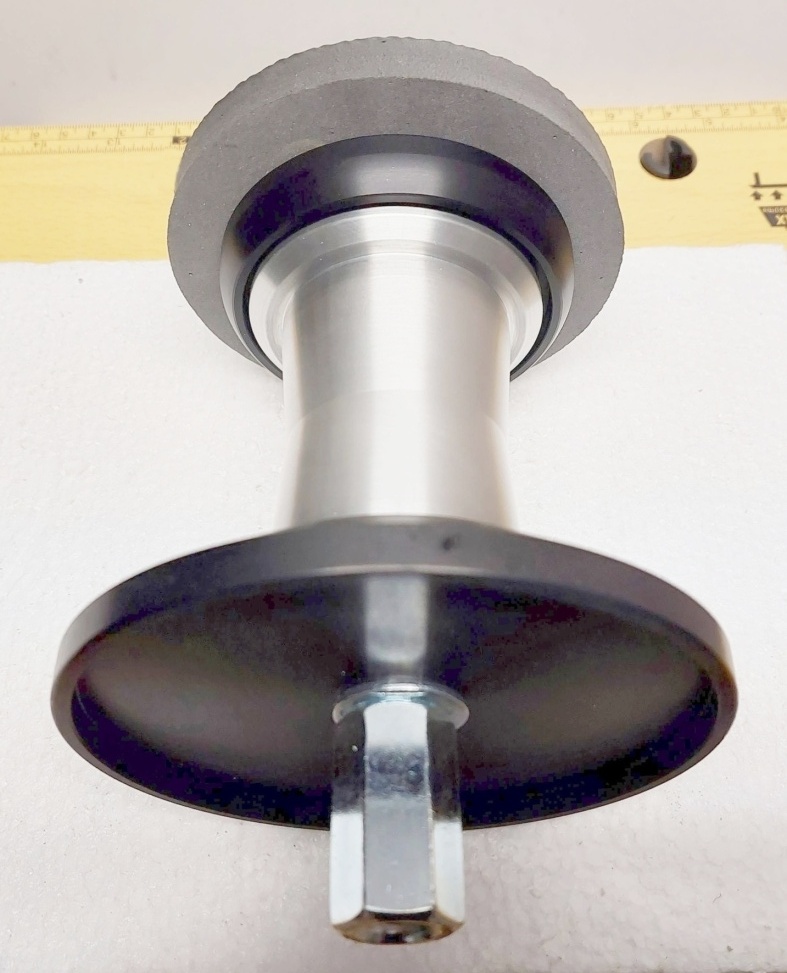
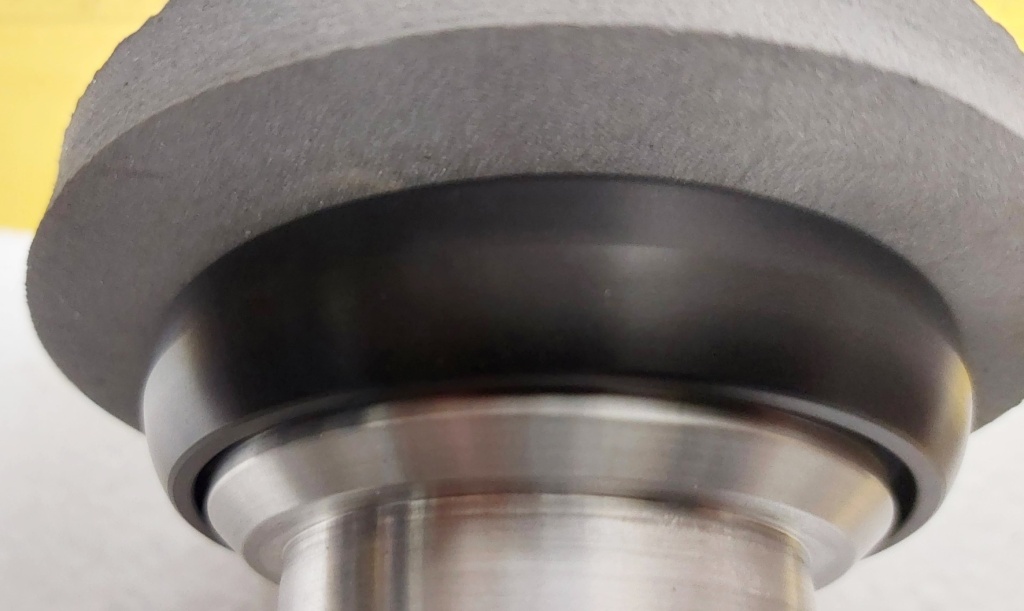
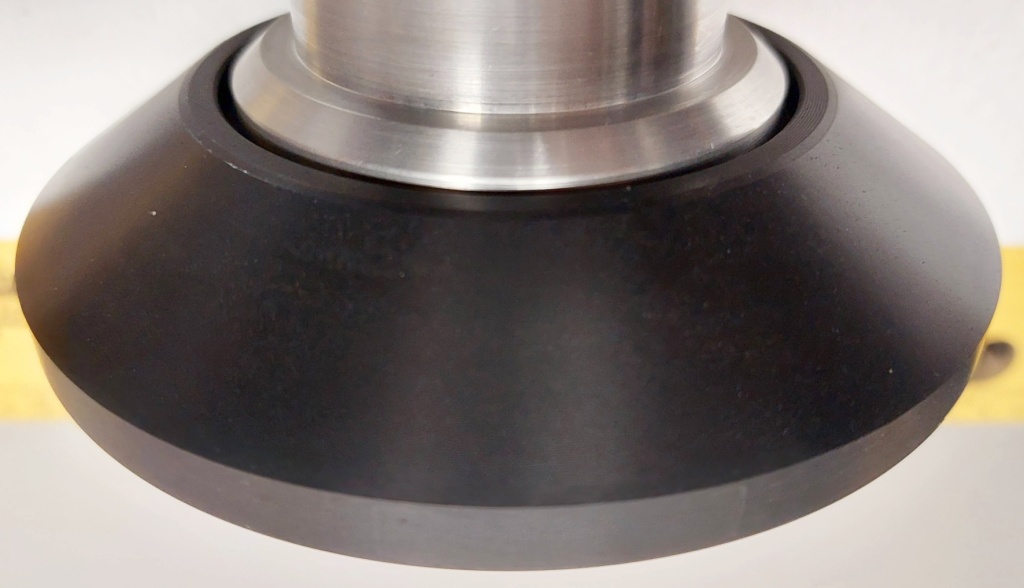
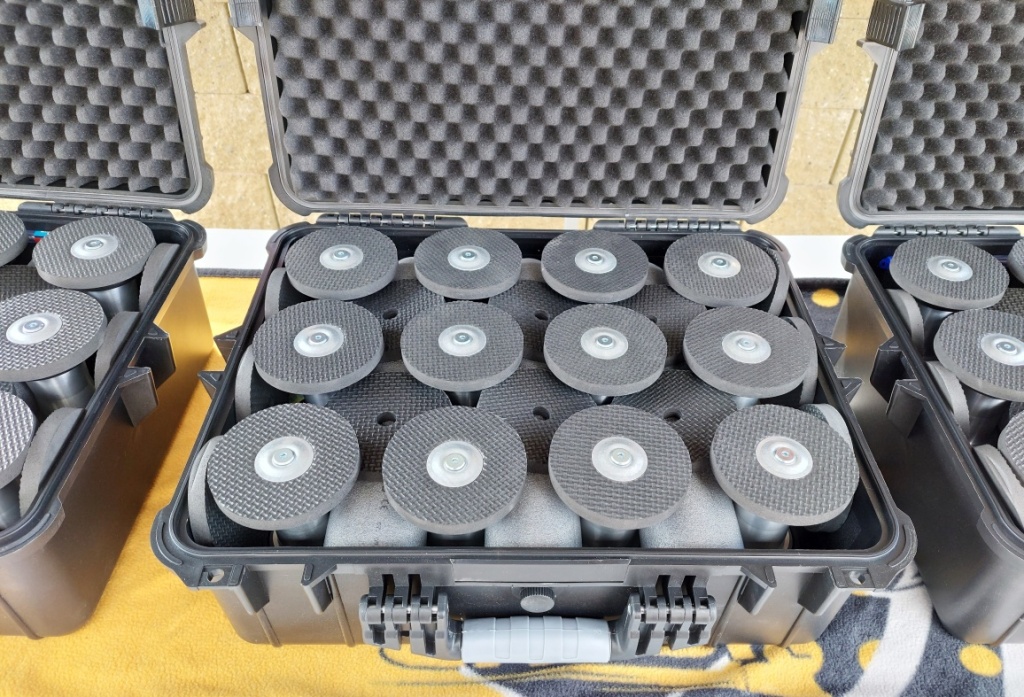

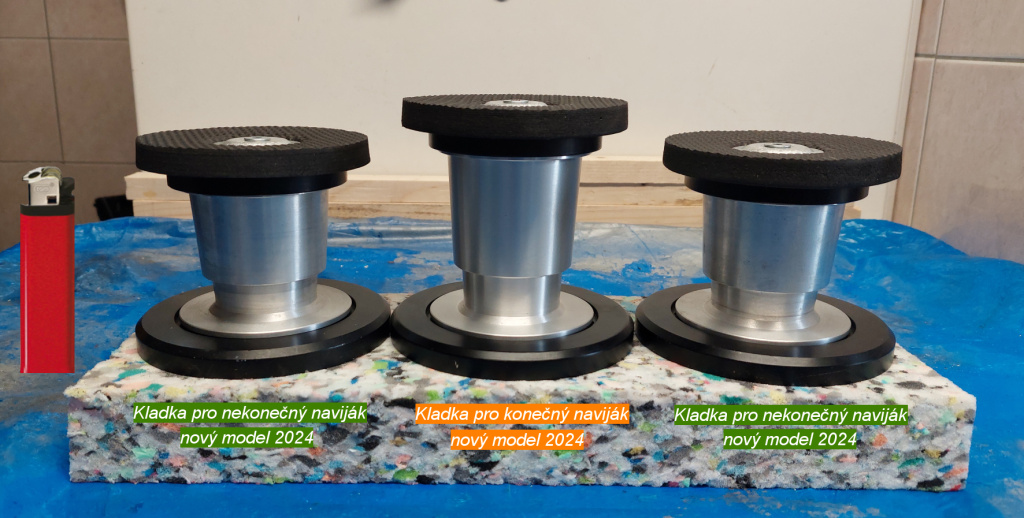
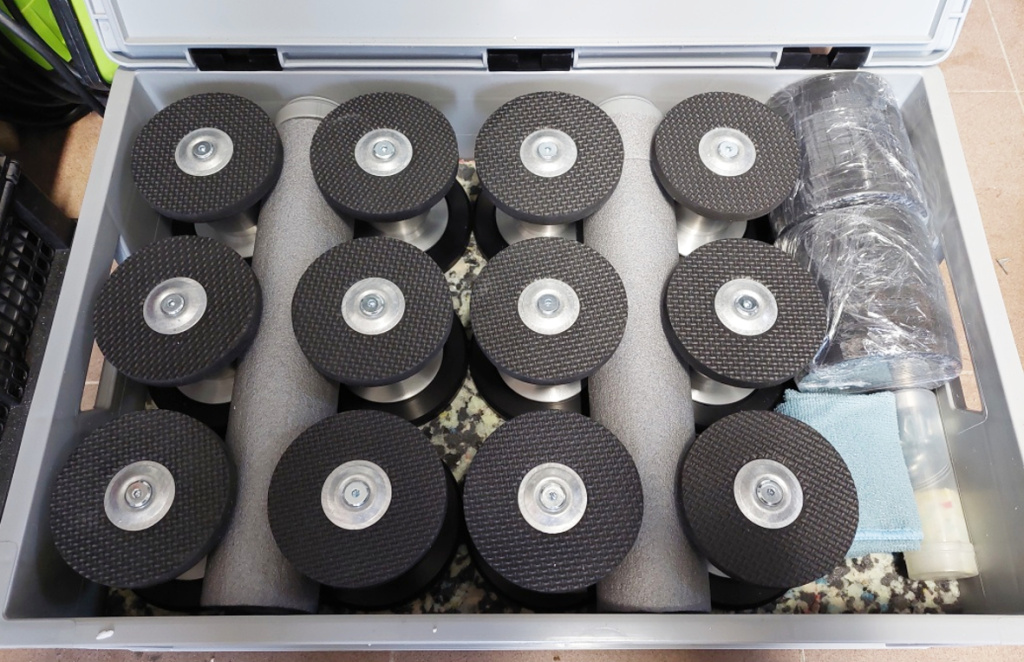
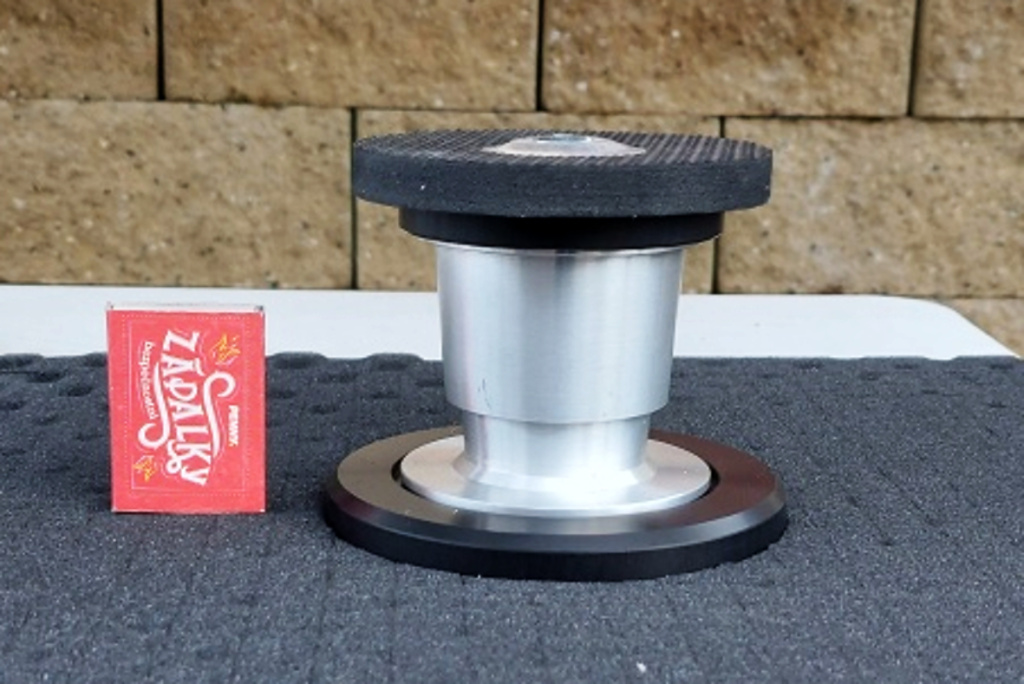
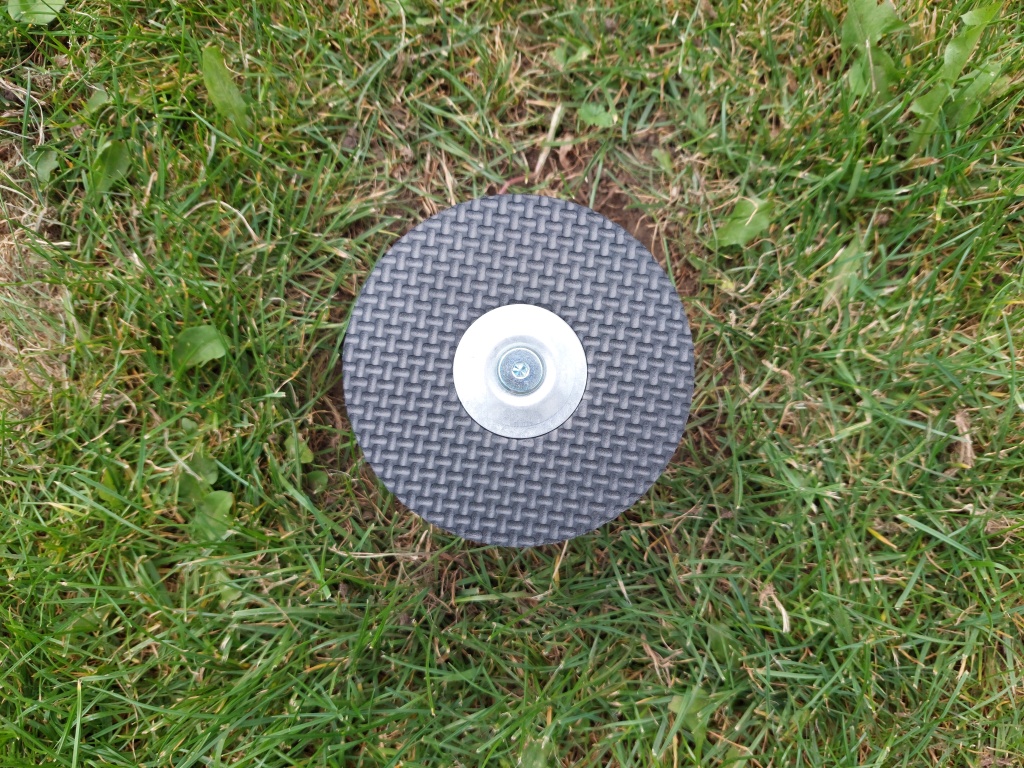
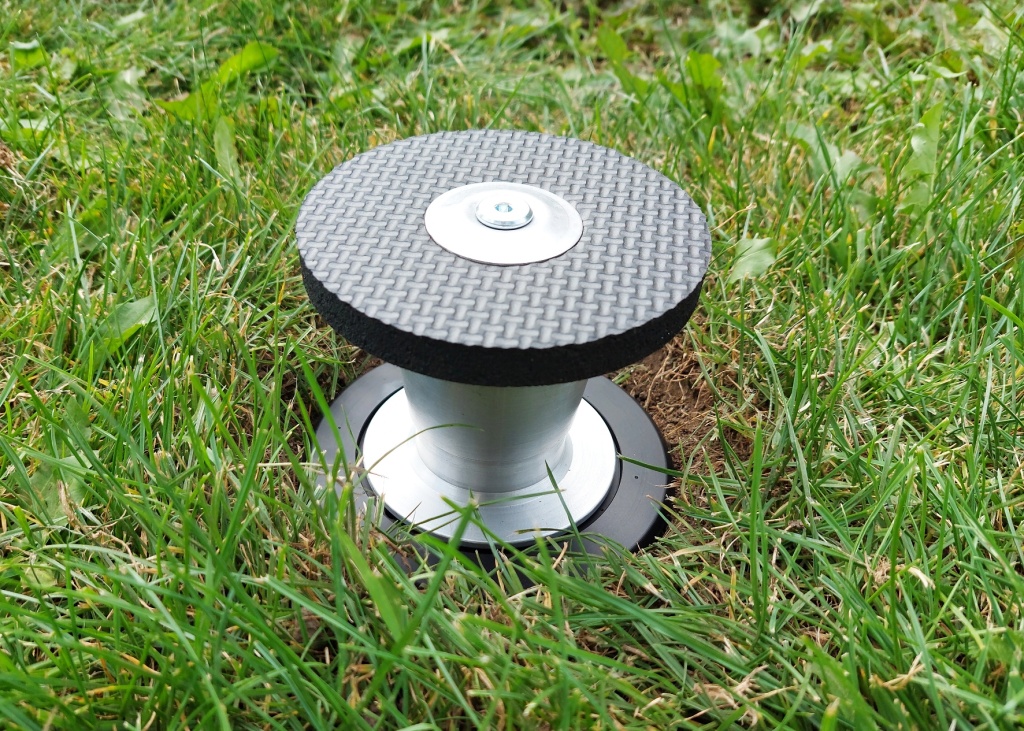
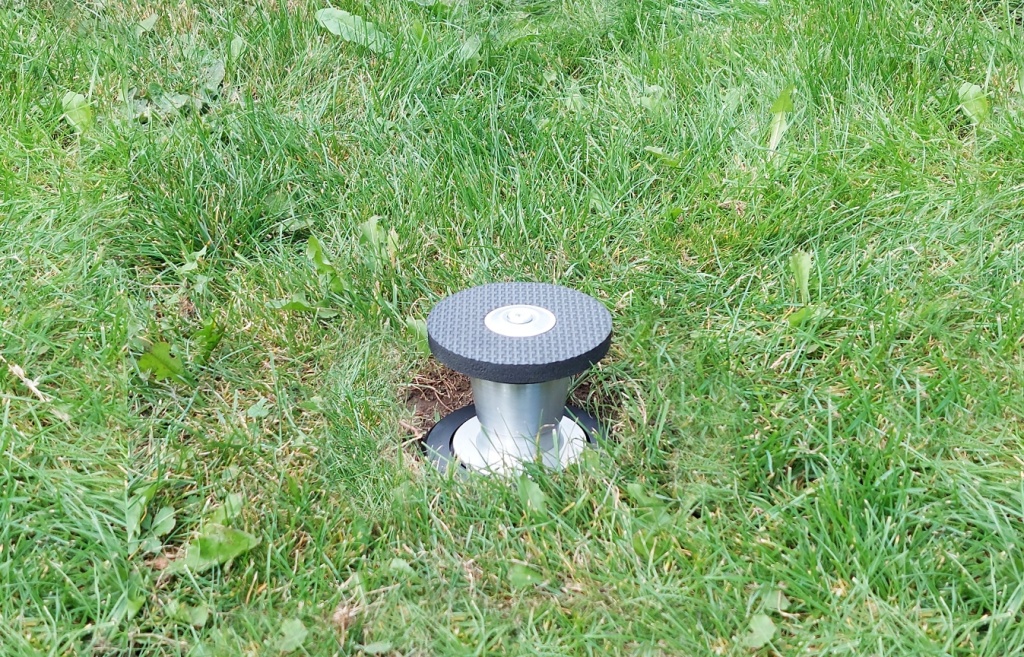
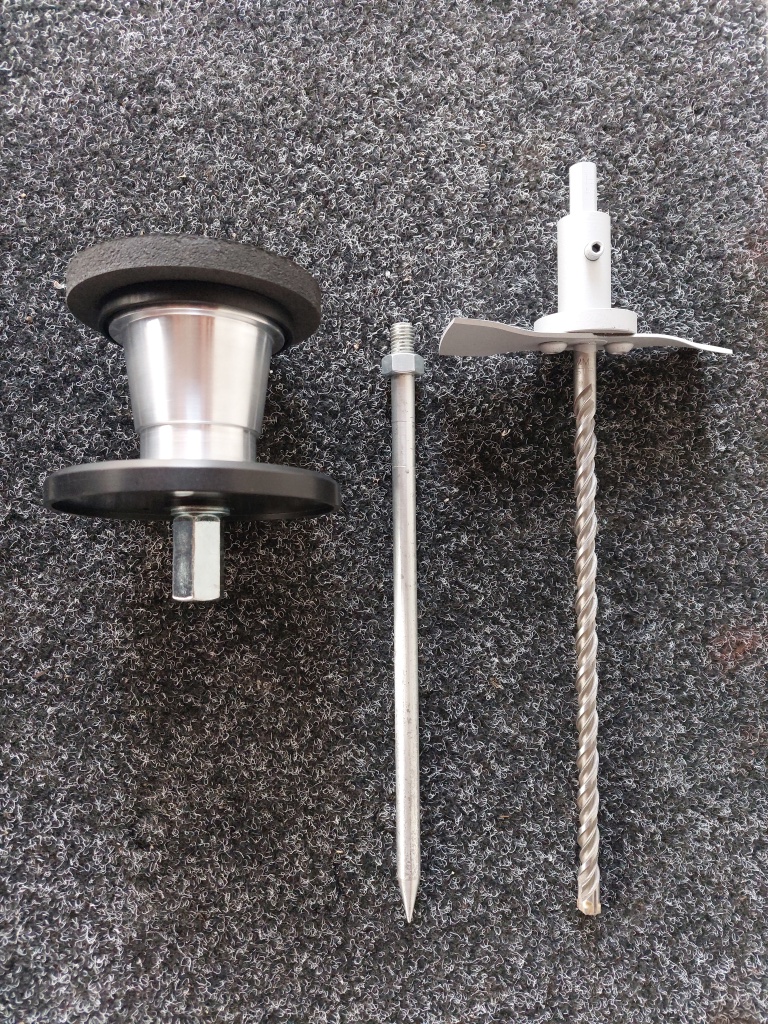
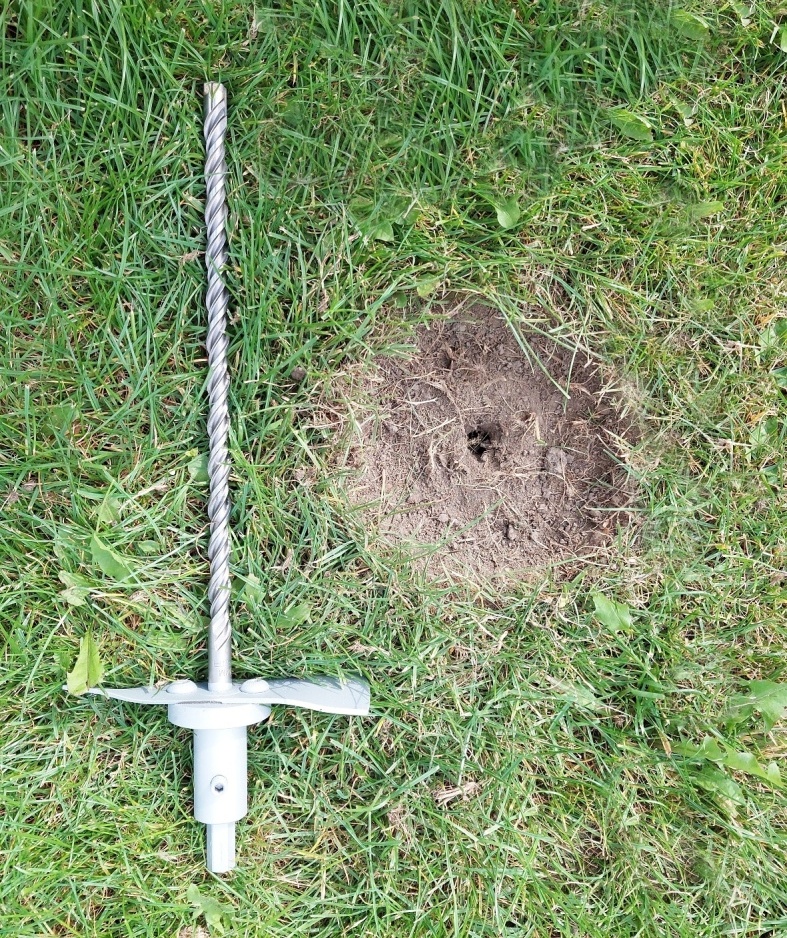
2. What material are the pulleys made of?
The pulleys are 90% made of duralumin for machining, which is the middle category of material properties. It is sufficiently strong, resistant to wear and temperature and the required precision in hundredths of millimeters is achieved during machining. Too soft a material is difficult to machine, deformable due to its elasticity and has a high wear rate. On the other hand, hard material is also difficult to machine and tends to crack under pressure and temperature differences. The rest, about 10%, such as nuts, bolts, washers, bearings, spikes are made of steel (see pictures).

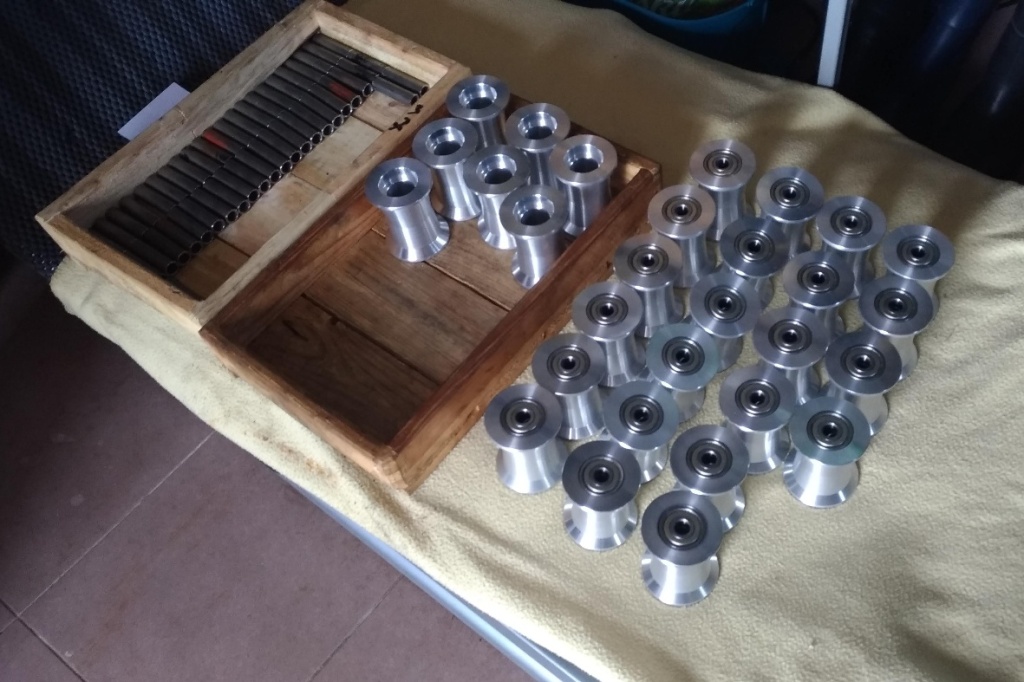
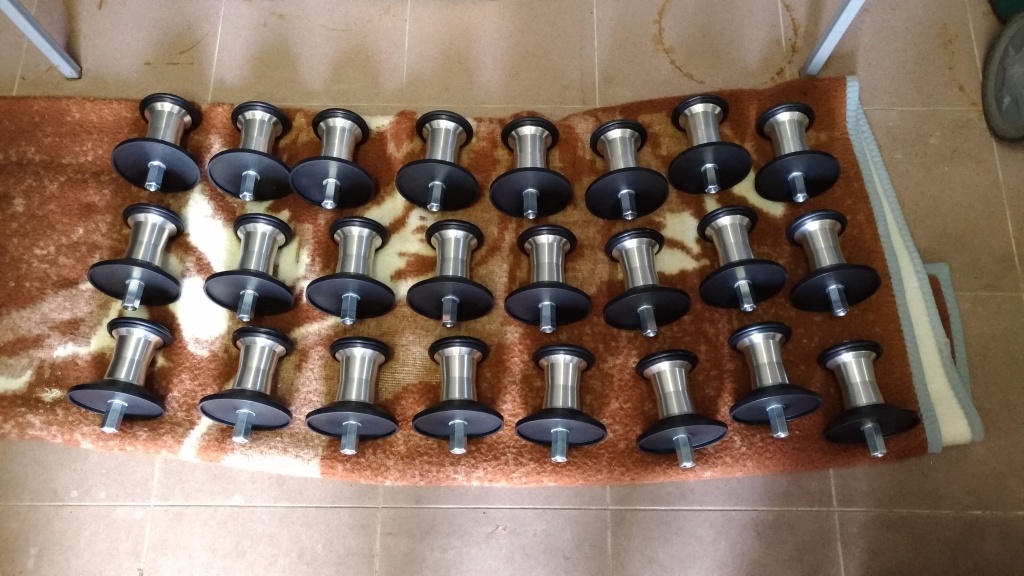
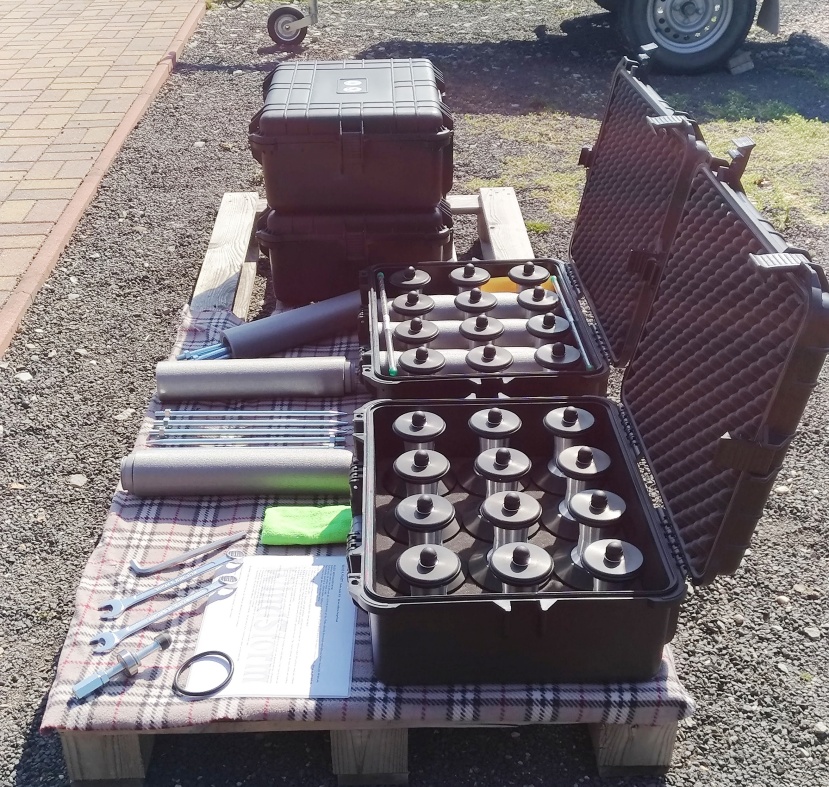
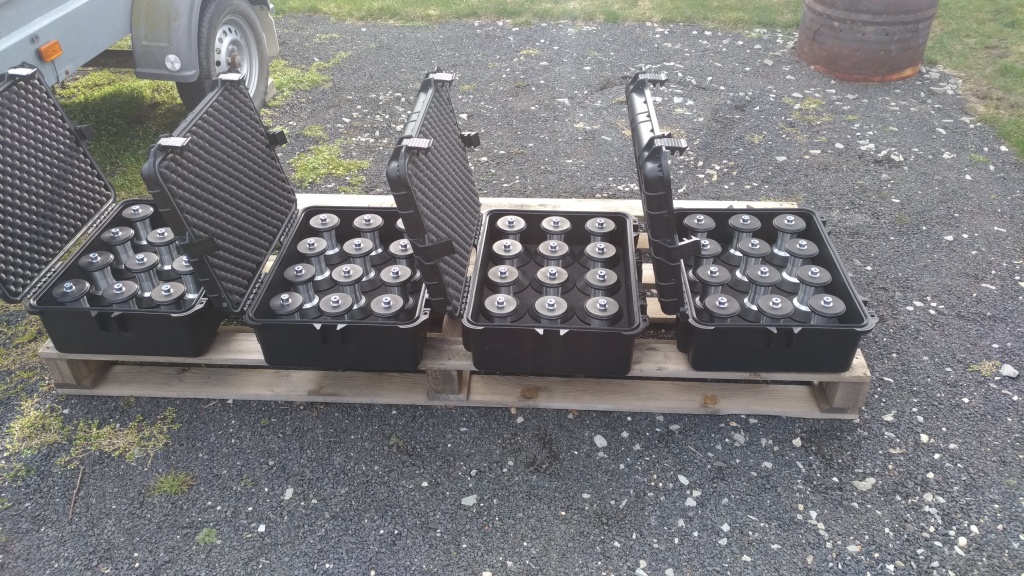
3. The pulleys look very simple, the modifications are rather cosmetic. Is this really the case?
This is the big mistake assumption. It takes a lot of work to invent something, but several prototypes are always made in succession. The pulleys always undergo tests, which usually show that something needs to be changed. After all, this year’s new model has been tested for more than 1 year on coursing, hunting breeds and bird of prey. And yet, before the launch of the new model we adjusted one dimension by 2 millimeters. (see pictures)
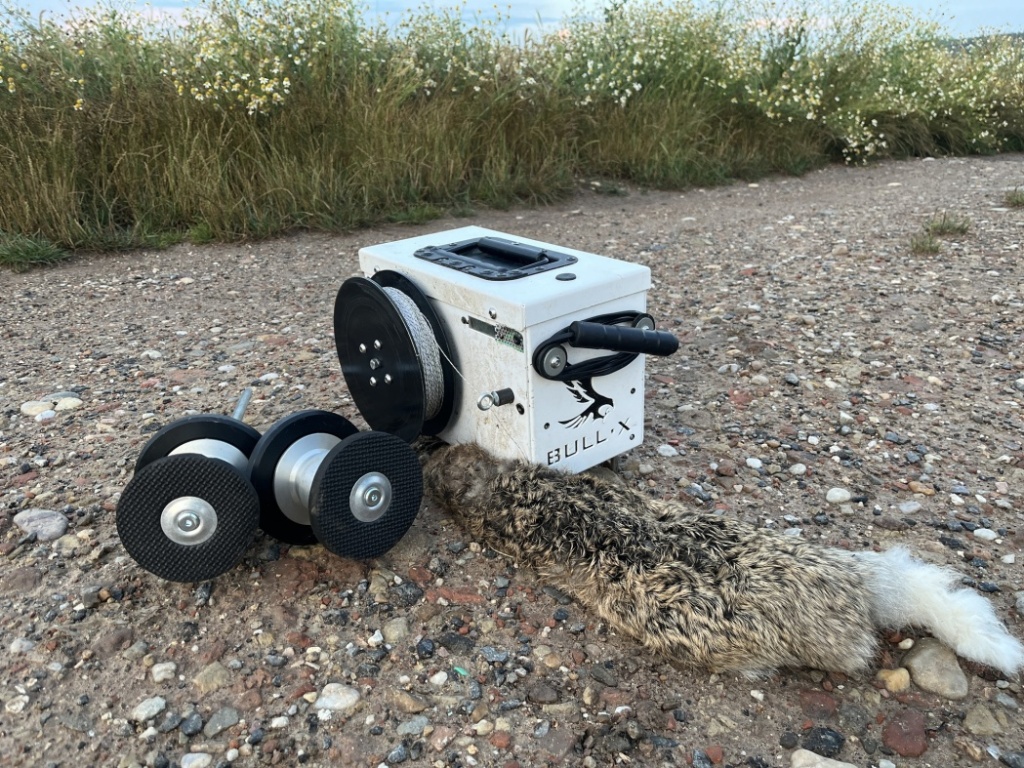
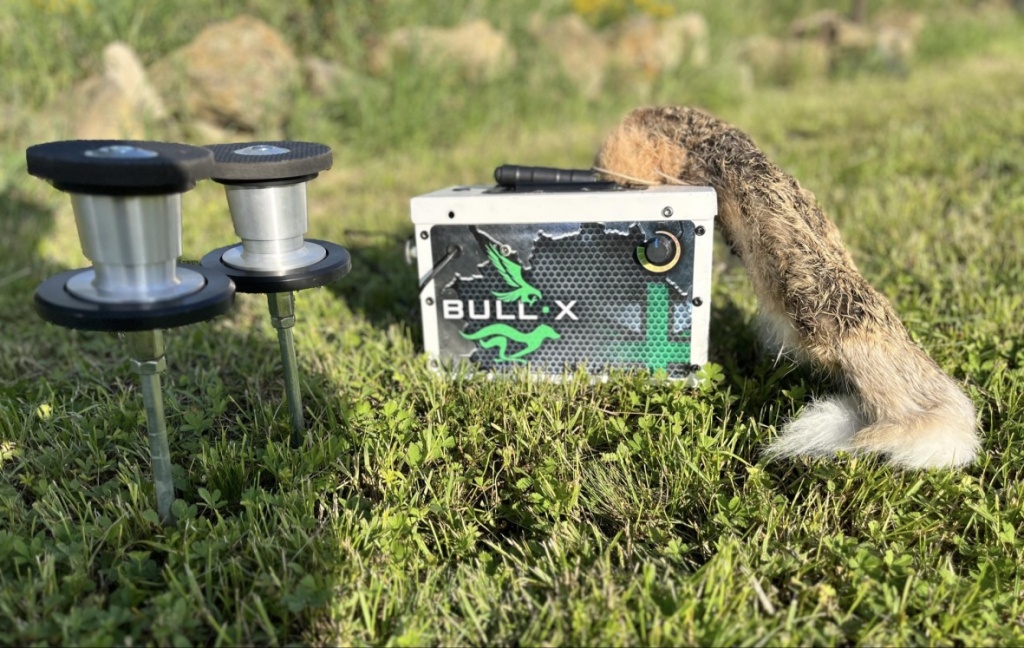
It should be noted that the price of each piece of prototype pulley always comes out about 2x higher. And I’m not talking about prototypes that were produced and not that they were bad, but due to their production they would be very expensive or have a lower lifetime. (see pictures)
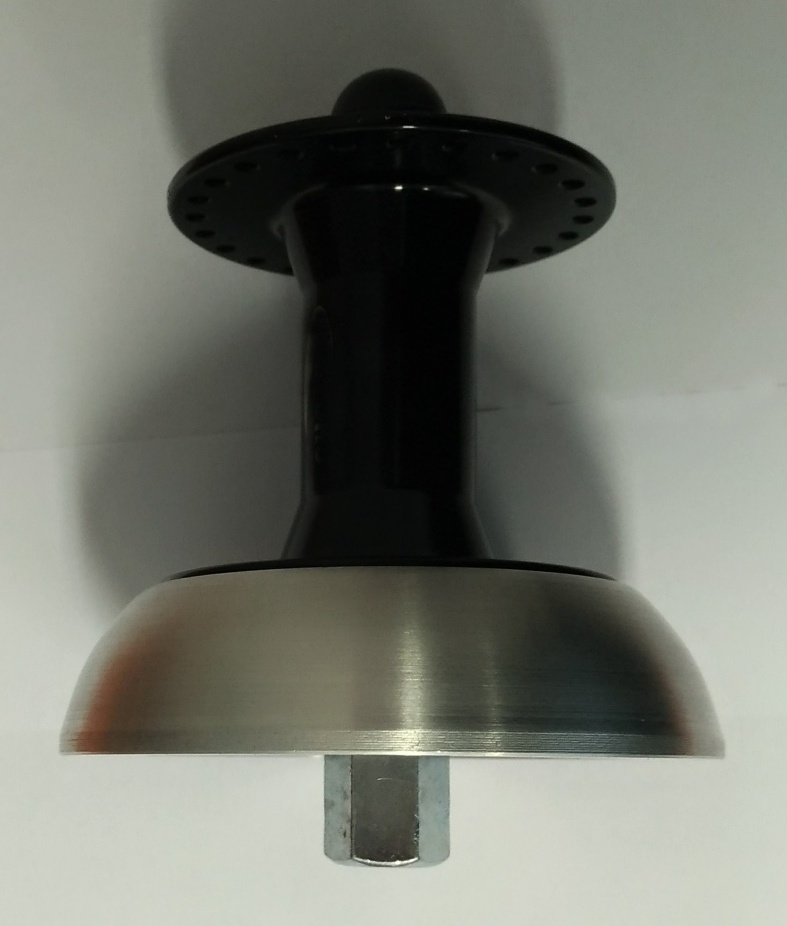
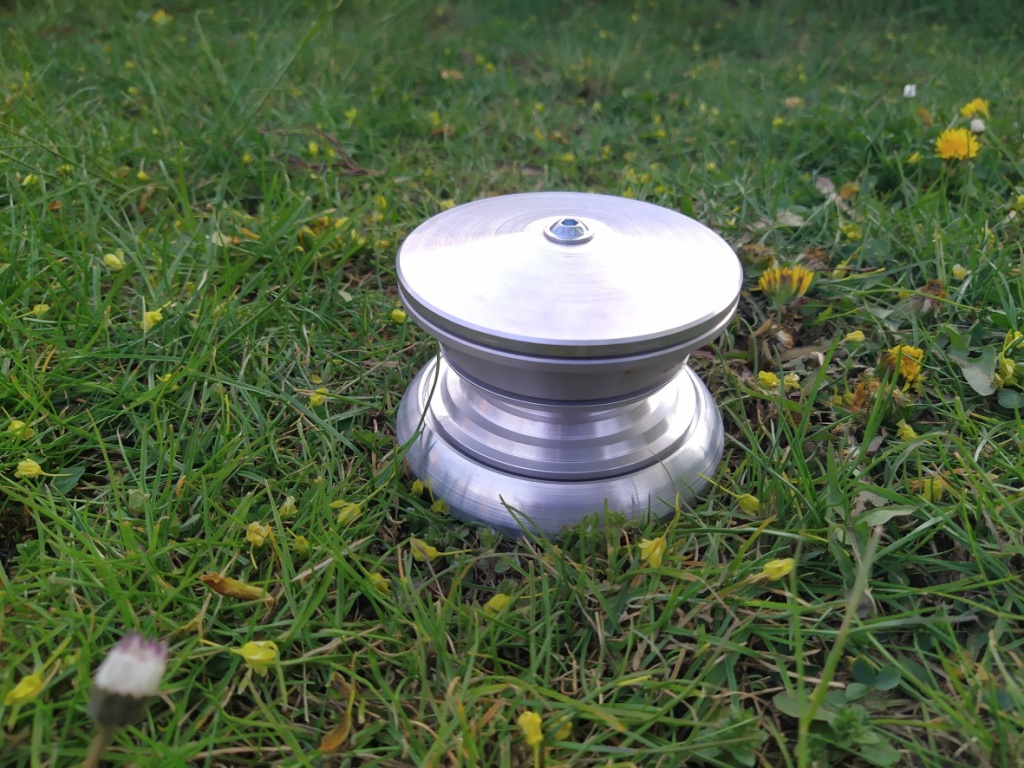
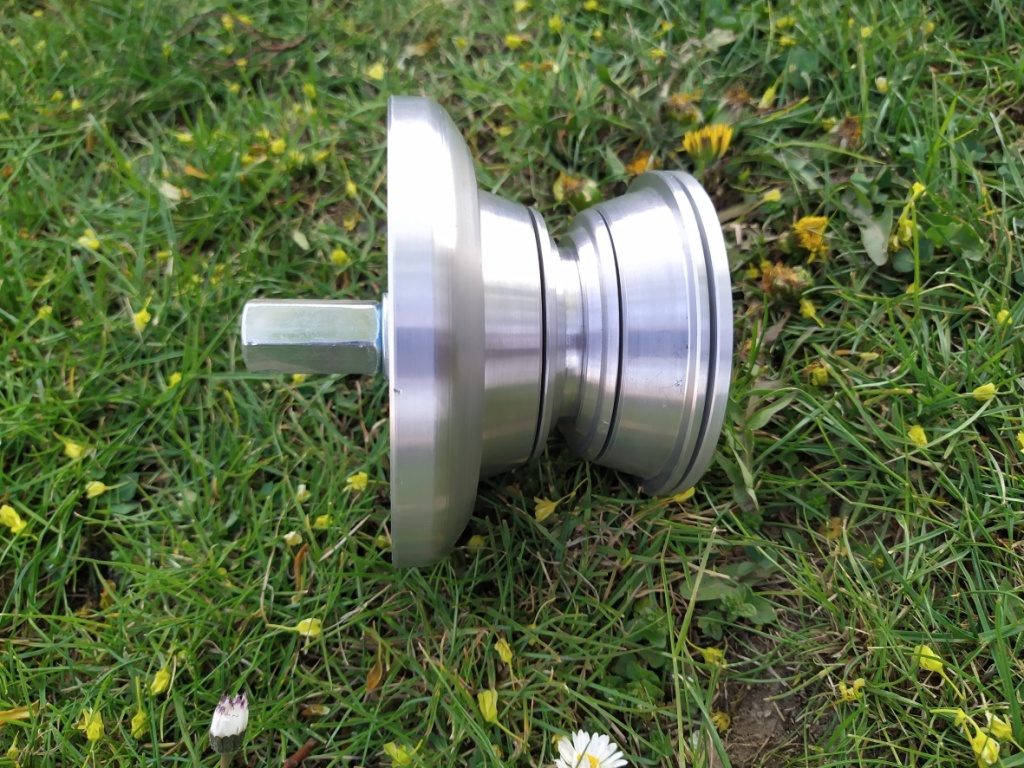
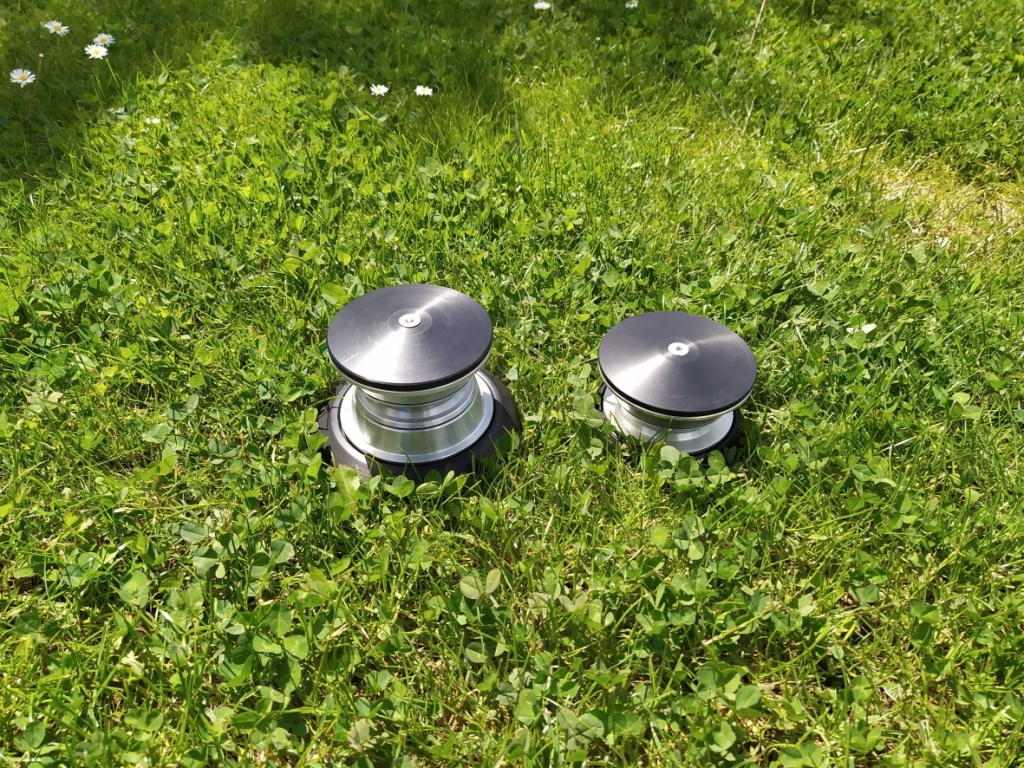
4. What is the reason for the higher price of the pulley?
It’s simple, the primary reason is the machining of the duralumin parts on CNC machines to hundredths of millimeters. These parts are then treated with a matt anodizing process, both to protect them and to ensure that there is no glare, which is prohibited by the rules. The steel parts are treated by galvanizing and some of them must undergo a machining treatment before that. The bearings used are high speed for long term use, maximum at 12,000 rpm. On these pulleys it works out that e.g. a speed of 30 km/h is approx. 3,000 rpm, 50 km/h is approx. 5,000 rpm, etc. The service life of the pulleys is therefore really long. Of course it depends on how the owner treats them.
5. Is it possible to negotiate some kind of discount when buying?
In the past I have offered 5% and 10% discounts as part of quantity discounts. The new 2024 pulley model is about 17% more expensive than previous models. The material is based on larger diameter duralumin and there are more CNC machine operations due to the substantial shape modification. In addition, material has become more expensive and payments to subcontractors have also increased due to inflation. Conversely, due to the fall in the exchange rate of the Czech Crown (koruna), the exchange rate is more favorable for foreign customers. In order to keep the price increase to a minimum, I had to take measures to find more advantageous material suppliers and sacrificed part of my business margin, resulting in a price increase of only about 7%. But I was left with no room at all to create price advantages. Production must generate at least a small profit. Buying pulleys, given their durability and quality, is an investment with a very good return.